Achieving a circular economy for packaging is held aloft as the ideal the industry should be chasing. But what are the realities of the current situation in Australia? Lindy Hughson spoke to local recycling companies to find out.
The journey towards a circular economy in Australia’s packaging industry is marked by innovation, collaboration, and significant challenges. Local recycling companies APR Plastics/ APR Kerbside, Close the Loop, iQRenew, Martogg and Plastic Forests are among those driving the change. They share common goals and a commitment to advancing circularity, but they also highlight the need for strong government support, stable market demand, and industry engagement.
CONTRIBUTION AND CHALLENGES
APR Plastics is investing in infrastructure for recycling soft plastics, including optical sorting and pyrolysis technology to convert multi-layered plastic packaging into pyrolysis oil. “Refineries, polymer plants, and packaging companies are already here,” says Darren Thorpe, managing director. “What we need is high-quality pyrolysis oil to replace fossil crude oil.”
Parent company, Australian Paper Recovery, is also expanding its cardboard recycling capacity, while APR Kerbside is progressing its glass-out initiatives for cleaner recycling outputs.
Focusing on plastics, Thorpe highlights three major challenges in advancing circular packaging solutions. First, sourcing feedstock. “As all multilayered plastic packaging currently goes to landfill, we are starting from a base of zero. We need to find it and divert it from landfill,” Thorpe says. Securing downstream partners is also critical, especially for working with pyrolysis oil, as refineries require consistency and safety. Finally, regulatory compliance adds complexity. “We’re learning a lot about compliance measures for advanced recycling in Victoria, which will put us in a great position to expand.”
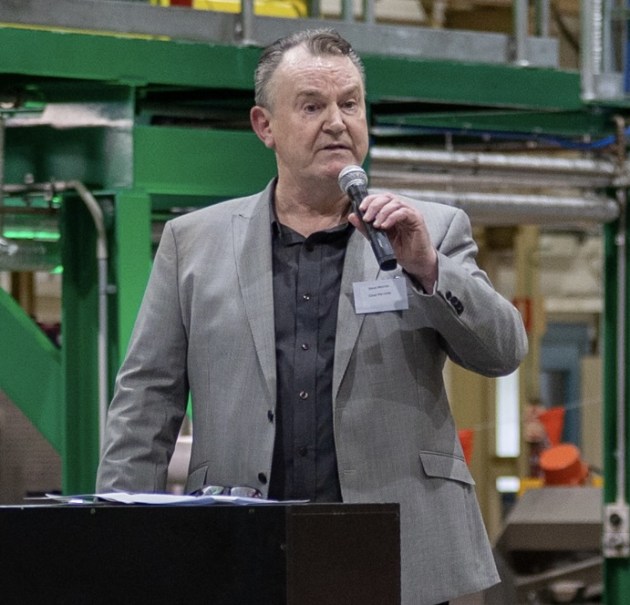
Close the Loop is living its mantra of “collecting today – creating tomorrow” leading collection and recycling programs for mixed post consumer soft plastics. “We’re not just putting recycled packaging materials back into Australian supply chains, we are doing it in partnership with Australian businesses and government via Circular Contracts,” says Steve Morriss, head of Circular Economy. A Circular Contract is where all parties share responsibility for buying products made from their own waste.
The biggest challenge, he says, is that packaging is not designed with the end of life in mind, making it impossible to efficiently recover single polymer types from post-consumer mixed soft plastics at a standard required to go back into food grade packaging. Close the Loop recommends widening the scope of the APCO Packaging Guidelines to include the use of plastics recovered from food packaging in non-food grade and even non-packaging applications such as tubs, crates, pallets, and wheelie bins.
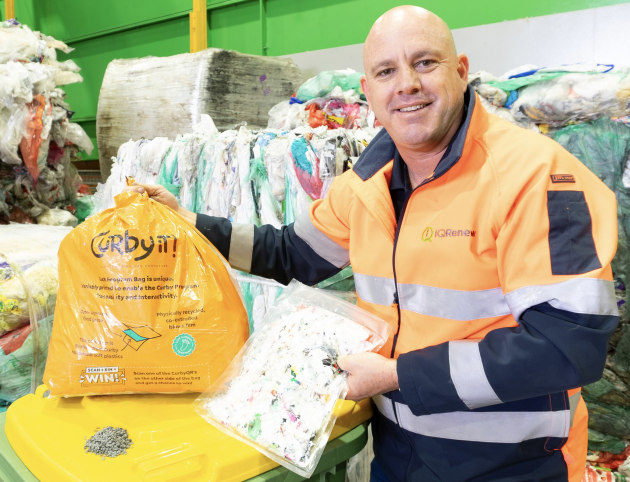
iQRenew has focused its efforts on developing recycling and processing capabilities for post-consumer soft plastics. Its Soft Plastic Engineered Commodity (SPEC) facility is the country’s first purpose-built site for sorting and processing 100 per cent post-consumer soft plastics.
MD Danial Gallagher says, “Through advanced mechanical recycling processes, the facility is the missing link in Australia’s recycling infrastructure.”
The facility is currently configured to process soft plastic legacy stock, Curby ‘bag-in-a-bin’ from customer councils around the country and potential future ‘return-to-store’ programs.
Despite progress, building a stable market for recycled materials remains a challenge for iQRenew. “The industry’s hesitance to adopt recycled resin products is a barrier,” Gallagher says, emphasising that a consistent demand for these materials is essential to making circular solutions economically viable.
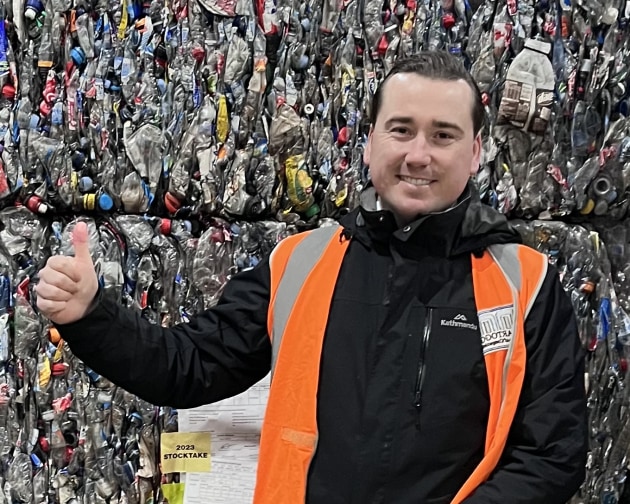
Martogg has a long history in recycling and sustainability, particularly with its rPET extrusion line introduced in 2016. Martogg’s capacity for food-grade recycled PET and HDPE is now more than 35ktpa, and the group’s washing and flaking capacity for local bale is scalable to 40ktpa.
“Our focus is on providing Australian-made recycled resins for the local manufacturing industry,” says Ramage. He highlights that a key challenge is convincing brand owners to adopt Australian-sourced recycled content, with many packaging products imported but the waste burden falling on local systems. Another hurdle is the perception of ‘downcycling’ in the industry, where recycled content is applied to non-packaging applications. Ramage believes supporting applications beyond packaging will be necessary to achieve high recycling rates. “Recycled content should be preferentially available for circular applications, but targets of 20-30 per cent recycled content indicate we need applications outside of packaging,” Ramage explains.
Plastic Forests is collaborating with numerous companies to recycle large mono streams of used flexible plastics. It processes up to 60,000 kilograms of flexible plastics each week, turning them into finished products distributed through hardware stores, to farmers for fencing, and to infrastructure projects such as underground cable protection for solar and wind farms.
Despite its capabilities, Plastic Forests currently operates at only 30 per cent of its production capacity. High costs and limited retailer support are primary challenges, says MD David Hodge.
“Labour, energy, and transport costs are all higher in Australia, making it difficult to compete with low-cost imports from Asia,” Hodge says. Without mandates for Australian-made recycled products, he notes, the lowest-cost producer often prevails. Another issue is retailer support: “If recycled products aren’t available on shelves, sales won’t happen,” Hodge explains, calling for government incentives to ensure shelf space for Australian-made recycled products.
GOVERNMENT POLICY REGULATORY REFORM
At a time in our industry when government is resetting its policy on packaging waste and proposing regulatory reform, the recyclers are of one mind that government policies can play a transformative role.
APR believes that including soft plastics in kerbside programs and establishing a plastics stewardship scheme to cover collection and recycling costs are essential next steps. “Expanding kerbside recycling could significantly increase the feedstock for pyrolysis,” says Thorpe. He also suggests looking to Europe as a model: “Their landfill diversion rates and sophisticated recycling systems show what’s possible with clear policies and enforced timelines.”
iQRenew supports an extended producer responsibility (EPR) scheme for soft plastics to fund recycling across the value chain. “EPR schemes ensure the entire value chain is adequately funded, from manufacturers to recyclers, and encourage investment in recycling infrastructure,” Gallagher explains. He advocates for policies that encourage recycled content buy-back through circular procurement.
Close the Loop anticipates that new legislation will further align brand owners with circular economy principles. “Government intervention strengthens our position, ensuring brands have a licence to operate in a modern economy,” says Morriss. Regulations that distribute responsibility across the supply chain, he says, will drive meaningful change in managing packaging waste.
Martogg argues that export bans on plastics are only part of the solution; protection from cheaper imported alternatives is also necessary to support local recycled content. “If local recycling were the most cost-competitive, we wouldn’t be exporting,” says Ramage. He calls for mandatory recycled content requirements and expanded demand for recycled materials beyond packaging to achieve circularity.
For Plastic Forests, government intervention is critical for addressing high costs and boosting demand for locally recycled products. Hodge suggests penalties for virgin resin imports and incentives for purchasing Australian-made recycled materials. “We need ‘refundable tax offsets’ like the Australian film industry overseen by the ATO to promote circularity,” he says, envisioning a government program to support such initiatives.
Australia’s recycling companies are pushing for transformative change. Stronger government policies, market demand, and industry collaboration are essential for realising a truly circular economy for packaging. These companies are ready to meet the challenge – if supported by clear and actionable strategies.
This article was first published in the November-December 2024 print issue of PKN Packaging News, page 18.