A study from Forrester Research found that while 74 per cent of firms say they want to be data-driven, only 29 per cent say they are good at connecting analytics to action. Here Darcy Simonis, industry network leader for ABB’s food and beverage segment, explains how to avoid being overwhelmed by big data.
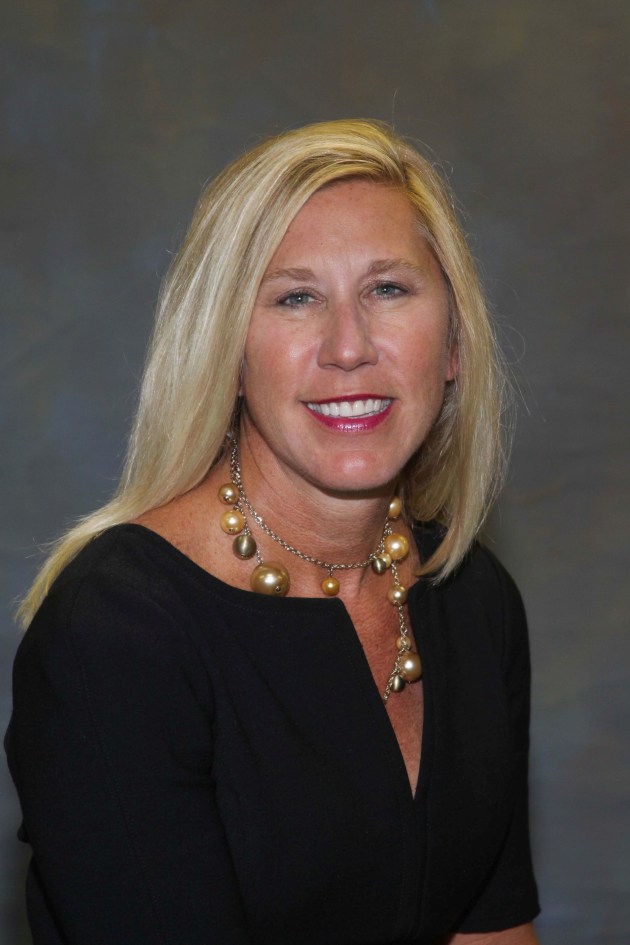
Food manufacturers understand that the future of their industry is data-driven. Smart sensors are now widely used across industry applications, providing insight into processes and allowing manufacturers to collate more data for analysis. As production becomes increasingly continuous and profit margins become finer, food manufacturers that are on top of their data will inevitably be more flexible and be agile to react to issues as they arise.
Having more data can be helpful, for example, if smart sensors, such as the ABB Ability Smart Sensors, alert an operation manager of a failing motor before it is in a critical state, then they will have more time to create a plan of action that minimises downtime and overall disruption. But maintenance is just one aspect of this development.
Harnessing data across the facility can support numerous aspects of manufacturing, from balancing conveyor belt throughput to ensuring continuous optimisation. However, if every system is constantly supplying information, it can be hard to discern which data streams to pay closer attention to.
Computers and data processing software can act smarter than ever before. They can discern trends and carry out deep analysis that can aid operation managers and many others in production environments. However, the computerised systems are not yet capable of understanding exactly who to send the data to and as such, it helps to have specialists available to make sure the correct person is receiving the right information and, most importantly, at the right time.
Having a system in place that can not only analyse the ever-growing amount of data while also having a group of specialists to review the data and determine who would benefit from it is, therefore, key. At ABB we offer the ABB Ability Collaborative Operations platform to make such a service come true. This solution consists of a group of dedicated centers with teams of specialists that look over a sites industrial data and then package the information in a way that most benefits the customer.
The ABB Ability Collaborative Operations platform provides businesses with access to specialists that they may not have in-house, such as cybersecurity. The results speak for themselves. In typical applications, an ABB customer reported an 84 per cent improvement in asset reliability over four years and a $22 million reduction in maintenance costs, as well as improved process availability, better throughput and improved safety.
For many years, integrating big data and connectivity was the goal for many businesses. Now that the technology has become more mature, it is important to use it to achieve actionable results. Using this technology to enable predictive maintenance and to ensure continuous production improvements must become the new target.
Those in the food and beverage industry need to be aware and agile within the ever-changing competitive landscape. Manufacturers ensuring that production systems are making the most of industrial data is a surefire way to improve production efficiency and remain at the top of their game.
Realising that you have bitten off more than you can chew is never a good sensation, especially when it could be the difference between the success and failure of meeting expectations. Having a system in place that means the business is never overburdened by information and that those in the relevant roles receive valuable and insightful information is not only a relief but in the hyper-specialised environment, is critical.