TNA says it helped UK-based Burton’s Biscuits double packaging speeds and assure quality, with a new installation that enabled the company to improve production efficiency, increase output, and reduce waste, while maintaining the highest levels of product quality.
Burton’s needed a high-performance packaging solution that could substantially increase packaging speeds to optimise production capacity for a new range of smaller, calorie-controlled bag sizes. The new single portion pillow bags contain Burton’s mini Maryland Cookies, and weight only 20g.
The solution here was to install three TNA Robag FX 3ci high speed VFFS packaging machines. This system offers “unmatched” throughput rates and are capable of producing 200 bags per minute, with wastage is low as 0.1 per cent, TNA says.
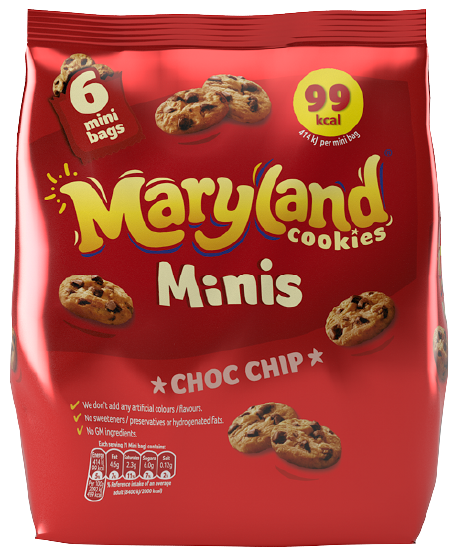
“Because consumer trends keep pushing companies to make smaller portioned packs, snack producers are having to consider either using more packaging machines to match the output of the over or fryer, or to slow down the entire production line. The TNA Robag FX 3ci can maximise throughput, delivering optimised packing speeds and allowing manufacturers to streamline their packaging process in a single piece of equipment,” said Simon Hill, TNA packaging specialist.
Aside from that, Burton’s needed a solution that could effectively combine high-speed production with consistent accuracy and reliability to achieve high packaging speeds while maintaining low reject rates. With the 20g pack sizes marketed as an under 100 calorie portion-controlled snack, it was critical for the end product to meet the targeted weight of six mini cookies per bag, and therefore the weigher must function to the utmost precision.
For this, TNA used its Intelli-weigh 120 Omega Multihead Weigher, which is says achieves weighing accuracy with a standard deviation of just 0.2g. The multihead weigher also maximises up-time with modular actuators, easy-to-use operator interfaces, and self-diagnostics.
All of this needed to fit with a limited floorspace. TNA says that VFFS equipment typically requires less plant space than horizontal packaging systems. The Robag also features what TNA says is the world’s shortest vertical product transfer from the scale to the pack.
“We already knew of the many successful installations of TNA machines in our sister sites, and TNA’s reputation for delivering the fastest vertical form, fill and seal packaging speeds in the industry. The system fits perfectly with our existing production line and has enabled us to increase our packaging line speeds, which are now running 135 per cent faster than the old equipment,” said Dean Donovan of Burton’s Biscuits.