Syntegon is setting new standards in capsule filling for the nutraceutical industry with the launch of its GKF Capsylon 6005. The latest addition to the GKF Capsylon series is already successfully in operation in the Asian market.
Syntegon says the GKF Capsylon 6005 differs from its predecessors primarily in terms of output and product yield – serving the need for higher production capacities of manufacturing companies.
“We are seeing growing interest in products like vitamins, proteins, and other dietary supplements” says Andreas Nuessle, product manager at Syntegon.
“The GKF Capsylon 6005 combines a significantly higher output rate with the flexibility of the range to fill powders, pellets, granules, and even special products. This makes it suitable for a particularly wide range of applications.”
The highest output with two dosing stations
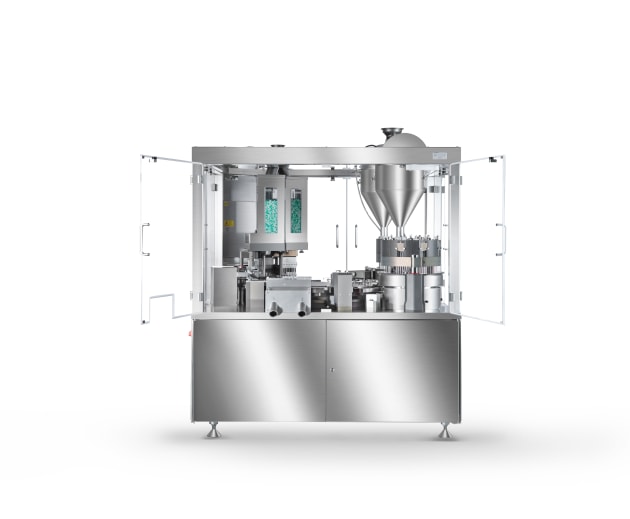
The GKF Capsylon 6005 is based on proven technology and features several innovations. With 360,000 capsules filled per hour, the output has more than doubled compared to the GKF Capsylon 3005 (175,000 capsules/hour), according to Syntegon. The high-speed capsule filling machine has 48 instead of 21 segment bores in four instead of two rows.
“The GKF Capsylon 6005 also features two dosing stations operating in parallel,” Andreas Nuessle adds. “This allows us to fill a larger number of capsule segments evenly without losing any time.”
Syntegon's patented slide-gate, which is used in the GKF Capsylon series by default, provides additional support. The slide-gate’s precise movements reliably cover the segment bores from below during filling. This results in a higher product yield and lower dust impact with overall higher filling accuracy. At the same time, the slide-gate technology offers manufacturers more flexibility by allowing the GKF Capsylon 6005 to process pellets or granules on the same dosing station.
Flexible format part changeover without readjustment
A further optimisation of the GKF Capsylon 6005 relates to format part changeover: the click system developed by Syntegon ensures significantly faster changeovers. No manual readjustment of the format parts is needed – the ideal prerequisite for processing a wide range of different products on the same machine in a time-saving manner. Operators can learn the use of the intuitive system with minimal effort.
Professional service worldwide
Together with Syntegon's high-shear granulators, fluid bed systems and capsule checkweighers, the new capsule filling machine can be combined to form a complete production unit. Syntegon also supports its customers with a comprehensive service portfolio.
Locally, Syntegon is represented by Nupac Industries, which has a knowledgeable and capable service team and supplies original Syntegon spare and format parts, which the company says always ensure optimum machine functions and smooth production. This minimises production risks and allows manufacturers to concentrate on their core business, Nupac says.