Canadian contract filler Ya Ya Foods has come to rely on KHS aseptic technology for its beverage filling requirements – and is planning to keep building on its €13.3m investment in KHS equipment to date.
Based in Toronto, Ya Ya Foods is run by president and CEO Yahya Abbas, who says he views himself as a facilitator – someone who doesn’t just wait for market opportunities, but anticipates them.
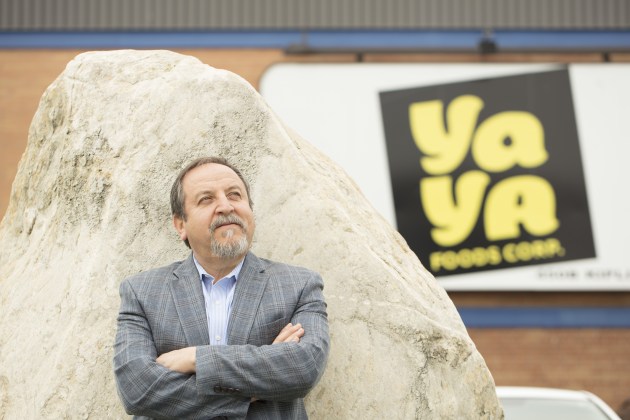
“I invest and generate capacity; our customers then come to us of their own accord. Our clients include the world’s top ten beverage brands – some of which have been our customers for 30 years,” said Abbas.
Ya Ya began with high-acid products such as juice, smoothies and tea, before moving to low-acid products such as vegetable and dairy milk products. Demand for quality in aseptic processing of these sensitive products is high, and Abbas says his maxim is not just to meet FDA or Good Manufacturing Practice guidelines, but to exceed them.
To this end, Ya Ya relies on its 250 qualified employees, plus modern measurement systems and manufacturing technology; its automated lines mean it only has about 65 machine operators working in production, who are responsible for a daily output of around 1.5 million units.
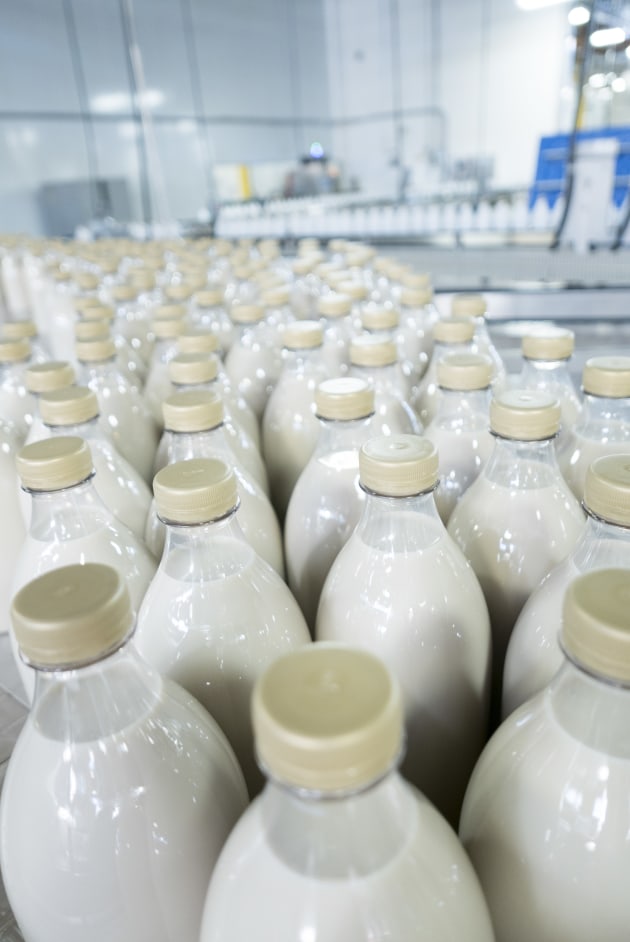
KHS predecessor Holstein & Kappert supplied Ya Ya with its first German machine in 1992, and Abbas in 2010 invested in his first aseptic filler from KHS proper: an Innosept Asbofill ABF 71 Twin, with a capacity of up to 24,000 one-litre bottles per hour.
The company bought a second 12,000-bottle-per-hour KHS aseptic line for small batches in June last year, installed another aseptic line in September, and plans a new joint project in 2020. According to Abbas, KHS aseptic equipment has won him over with its adherence to high hygienic requirements and its flexibility.
“Format changeovers in the filler area are quick and trouble-free. KHS gave us the best option back in 2010 – and nothing has changed in this respect. This is a very good system and our contact partners excel with their extensive expertise and many outstanding ideas,” he said.
KHS is a member of APPMA.