In what the company is calling an Australian first, BioPak has launched its PHA range, which it says is a “game-changing innovation set to revolutionise the home-compostable cup industry”.
PHA (polyhydroxyalkanoate) is an innovative material that is biopolymer, which is produced through a fermentation process similar to brewing beer, using renewable sources like plant sugars and vegetable oils.
After years of research and development, the final result is a cup that BioPak says truly aligns with the circular economy, and is now ready market its innovation at scale for the compostable packaging sector. It is made entirely from bio-based renewable resources, such as FSC responsibly-sourced paper and PHA lining, meaning the cup doesn’t contain any fossil-based materials.
PHA lined cups are home compostable at the end of their life, which bolsters BioPak’s home compostable range and its mission to empower consumers to manage disposal of their packaging waste at home.
Gary Smith, CEO of BioPak, commented on the significance of the company’s latest innovation and its capabilities for the future of compostable packaging solutions.
“We are incredibly proud and excited to be the first to bring this ground-breaking product to Australia,” he said.
“PHA has been a long time in the making, with our dedicated team working tirelessly to bring this product to market.
“As a B Corp, we are always striving to do better and be at the forefront of innovation and R&D, and today marks a historic moment for our industry as we take one step closer to circularity and reducing our impact on the planet.”
A notable factor of the innovation is that the PHA resin is certified marine biodegradable, meaning that it will break down significantly faster (it needs to biodegrade in marine settings in less than 180 days) than conventional plastic if it ends up in the ocean.
“This is a breakthrough in bioplastics. However, our products are not designed to be disposed of in the marine environment, so we won’t be advertising it on the cup,” Smith added.
“Its ability to biodegrade quickly is not a licence to litter but an opportunity to have an end-of-life solution for people with access to a home compost.”
Expected to launch commercially later this year, PHA will be certified home compostable to Australian and European Standards (AS5810 and NFT51-800), with BioPak PHA lined BioCups available in 8oz, 120z and 16oz single wall cups.
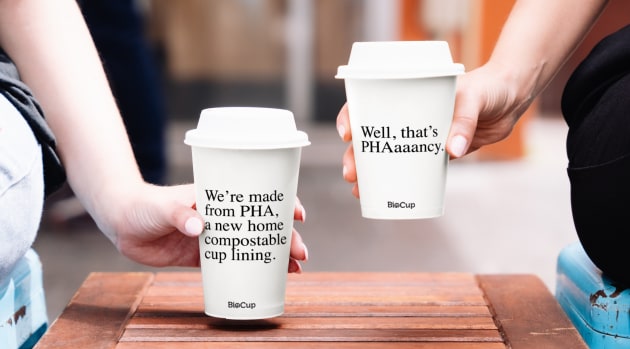