In this technical article for interpack 2020, Melanie Streich examines the latest developments in pharmaceutical packaging technology.
Chronic diseases are more widespread than ever before. In industrial nations, and increasingly in developing countries as well, they are among the most common and economically relevant health problems.
The health sector’s global economic factor is accordingly high, and simultaneously acts as leverage for the pharmaceutical industry, which invests a comparably high share of its revenue in research and development (R&D).
In light of global demographic changes, the industry’s development opportunities are excellent. People are living longer and more health-conscious lives – which further increases the high-tech sector’s growth outlook. Growing drug development requirements result in a parallel increase in systems and machine technology demands in the field of packaging and bottling medicines.
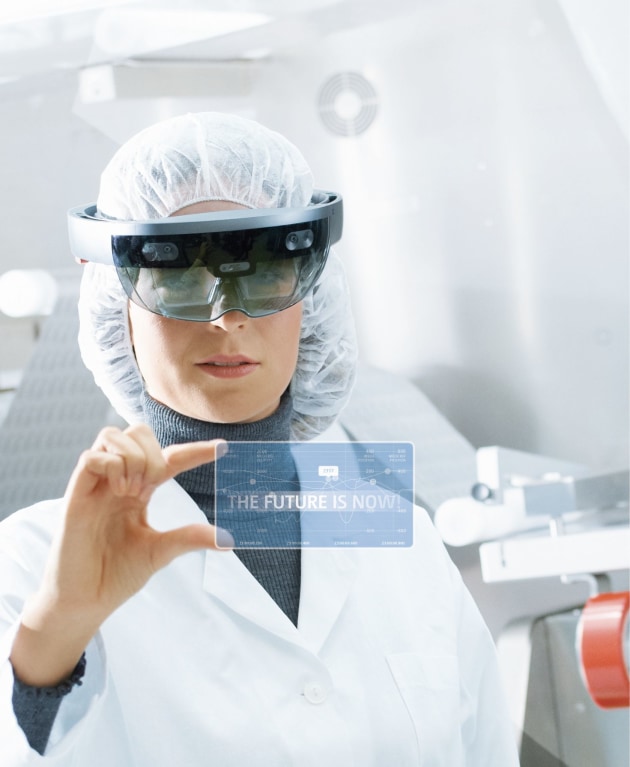
Photo: Uhlmann
“Today, pharmaceutical companies need integrated solutions. Machines provide the foundation for these. An extensive service offer and digital solutions in particular are gaining in importance,” explains Norbert Gruber, Chairman of the Executive Board at Uhlmann, which provides systems for packaging pharmaceuticals in blister packs, bottles and boxes. The German family business, which has more than 2,300 employees around the world, has accordingly positioned itself as an innovative and digitalised company at interpack 2020, the world’s leading trade fair for the packaging and associated process industries.
From 7 to 13 May 2020, the trade fair presents further cutting-edge solutions that the industry has to offer. As a focal point for pharmaceutical packaging, Halls 15 to 17 offer visitors the opportunity to find out more about innovative packaging and process developments for this specific industry. The other halls also showcase corresponding solutions: the approximately 1,000 companies with exhibits on Industry 4.0; digitalisation; automation; personalisation; track and trace; and many other interesting topics from the field of pharmaceuticals represent a significant share of the around 3,000 exhibitors at interpack.
Pharmaceutical market forecast
According to figures released by market research company IQVIA, global expenditures for pharmaceuticals are expected to increase to US$1.43tn by 2022. In 2006, by comparison, expenditures were US$658 bn. The highest amount is spent on cancer medication and biopharmaceuticals.
The reasons for this increase in market growth are quite apparent. Demographic change with a rise in older patients, and increasing urbanisation with a growing middle class, are the determining market factors for the pharmaceutical sector and the associated process and packaging industries.
The future of biopharmaceuticals
While more and more people in pharmerging countries are gaining access to traditional medicines such as painkillers and antibiotics, industrial nations are increasingly employing new, complex active ingredients and innovative treatments.
In the pharmaceutical sector, biotechnology is considered a key technology in the global fight against severe diseases such as cancer and autoimmune diseases. Their share in the medical market has almost doubled in the past ten years, and has thus become a decisive factor for the process and packaging industry.
Sophisticated processing
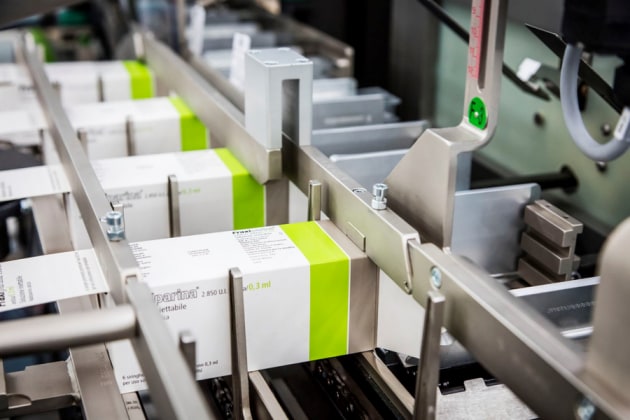
Photo: Marchesini Group
Highly effective medicine is accompanied by considerable demands on packaging and processing technologies, particularly with regard to bottling and packaging solutions. When manufacturing biotech medicines, avoiding contamination is essential. Special containment solutions aim to prevent said contamination.
Isolators are one such example. Liquid medicines can be processed under sterile conditions in vials. Pre-filled syringes also contribute to an increase in safety, as they help prevent dosage errors and also eliminate contamination when changing needles. In the hectic daily life of practices and clinics, pre-filled syringes and pens also save precious time. Authenticity checks performed on complex purification processes using combined sensor technology and mathematical models ensure that quality controls can be performed much more quickly with increased process accuracy.
Pharmaceuticals and packaging: True team play
When manufacturers launch new pharmaceuticals, they depend on the market and technology competence of machine systems and packaging manufacturers and processors. Time limits on patent protection require fast and flexible solutions that have to guarantee scale-ups from small laboratory amounts to high volumes in larger plants.
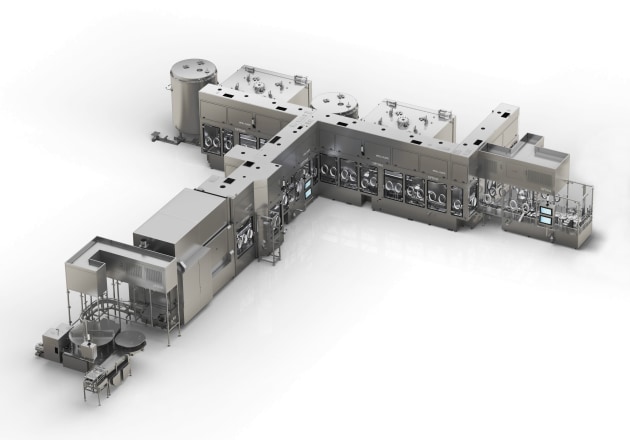
Optima is a single-source provider of packaging machines and bottling and production systems. To ensure that newly developed products can be launched as quickly as possible, Optima uses the CSPE method, which will be one of the company’s central topics at interpack 2020. This method reduces delivery times and significantly accelerates the commissioning of pharmaceutical systems.
“In light of increased development periods and costs on the one hand, and increasingly tough international competition on the other, the time between concluding the approval phase and launching the product has to be kept as short as possible,” explains Gerhard Breu, Chairman of Optima’s Pharma division.
At the same time, companies require reliable packaging machines and bottling systems that are easy to use and clean, and that can be retrofit without great effort. Pharmaceutical service provider Harro Höflinger provides support in the early stages. Its clean rooms and laboratories can depict extensive processes in a controlled environment, whilst test setups allow clients to check critical steps in advance.
“Our clients increasingly ask to test their own substances and critical conditioning products on machines designed by Harro Höflinger. Our clean rooms and laboratories are the perfect place to implement these tests. They allow us to recognise and minimise risks at an early stage – the basis for quick and safe scale-ups to commercial manufacture,” explains Stefan Mayer, Senior Director Process Services.
Protection against counterfeiting
In the pharmaceutical field in particular, strict legal provisions and guidelines apply that are of extreme importance for all parties involved in the process, and that at the same time mean tremendous investments for the affected companies. Since February 2019, prescription medicine in the EU has to be equipped with tamper-proof seals that ensure that the packaging has not been opened.
Serialisation on the packaging is now also a legal requirement. All affected packaging has to be equipped with a two-dimensional datamatrix code that uniquely identifies the medicine and confirms its authenticity. This code contains information on the batch number, the expiration date, the serial number, and the national reimbursement number.
These new regulations have far-reaching consequences. In individual cases, production facilities have to be expanded, constructed or modified to accommodate new serialisation units. The expansion of the IT infrastructure in particular is a true feat of strength for many companies and is associated with high costs.
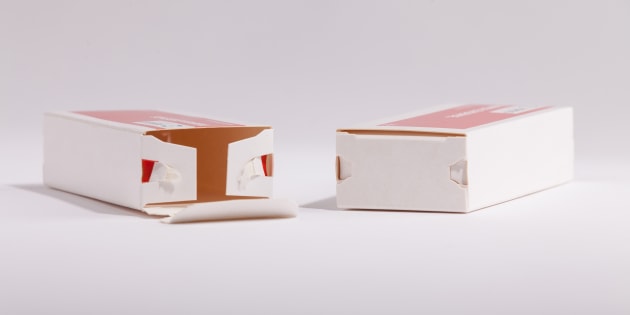
Körber Medipak Systems offers extensive solutions that protect patients against counterfeit medicine. Pre-serialised folding boxes with tamper-evident seals and targeted system solutions put a stop to counterfeit medicines in the legal value chain, as packages now visibly and unambiguously show whether they have been opened or not.
The silver generation
By 2050, global population will reach 9.7 billion people; a mere 50 years later, this number is expected to increase to 10.9 billion, according to the most recent UN global population forecasts released in June 2019. In 2050, every sixth person in the world will be over 65, with a total of 426 million people over the age of 80. This equates to triple the 2019 numbers, with 143 million people over 80.
These demographic changes also mean a rise in diseases that increasingly occur with age, including diabetes, rheumatism, multiple sclerosis, dementia, and Alzheimer’s disease. The affected patients require particular administration methods, depending on the type of complaint and symptoms. Pre-filled syringes and auto injectors help people with limited mobility regularly administer their medicine themselves.

The packaging industry offers smart packaging for patients whose sight and hearing are dwindling or who are losing their finger strength and motor skills. One of these innovations was created by pharmaceutical technology provider Romaco Siebler. In cooperation with foil experts Huhtamaki, Romaco Siebler developed Push Packs, which are equipped with special, accessible features and allow patients to easily push tablets out of the foil.
“Push Packs are an affordable alternative to cold-formed aluminium-aluminium blister packs (AI/AI blister packs). As the packaging foils are a lot thinner, they require less material. This reduces packaging costs in direct comparison by up to 60 percent,” calculates Jörg Pieper, CEO at Romaco Holding.
Tailor-made medicine
Personalised medicine will change the global health system considerably in the years to come. Studies have shown that more than 70 per cent of all pharmaceuticals currently in development have been customised to meet the needs of specific patient groups. In cancer therapy, individual medicine is already common and is to supplement standard therapies in future. Scale-out solutions for machines and equipment enable the production of smaller batch sizes. Here, existing equipment is copied exactly for other locations. This requires clearly defined processes and machine technology with a high degree of automation.
More and more pharmaceutical manufacturers require flexible bottling and packaging systems that allow them to work on small batches with maximum efficiency. Bausch+Ströbel has a compact solution in their portfolio: the modular VarioSys production system, which is also suitable for application in laboratories with small batch sizes.
“Flexibility is the first priority in all our designs. We achieve this by quick and easy module changes on the one hand and short cycle times when sterilising the isolator on the other,” explains Heiko Schwarz, who is responsible for the development of VarioSys in product management at Bausch+Ströbel.
Print your own tablets
Tablets fresh off the 3D printer are no longer a dream of the future. Spritam, a printed epilepsy treatment, became the first such medicine to be approved by the Food and Drug Administration (FDA) in 2015. 3D printing processes allow manufacturers to adapt products exactly to patient needs whilst reducing time and cost factors in production, as machine components no longer need retrofitting.
Compared to conventional tablet presses, printed pills can also be equipped with a more porous surface, which helps them dissolve more quickly and without additional liquid intake. They can also be equipped with more active ingredients. This particularly benefits patients who have difficulty swallowing and who depend on various tablets. However, experts say it will be quite some time before patients can print their own prescription medicine, with an individual formula put together by their doctor, in the comfort of their own home. The current fields of application are limited exclusively to highly specialised, individual medicine.
Convenience and safety
Personalised medicine is a field that particularly affects the hospital and care sector. To ensure that patients receive the right drug cocktails whilst relieving carers of the task of putting the necessary medicine together, tablets may be blister-packed ready for use.
Blister pack machines in chemists and blister packaging centres pack the patient’s individual tablet mix in an airtight and hygienic strip of sacs and simultaneously ensure that the individual doses are labelled and delivered in the right order. This prevents wrong dosages and ensures that patients do not take the wrong tablets by mistake.
Cost pressure and systems efficiency
Despite all the positive market developments in the pharmaceutical sector, we must not forget that even though the industry is growing, the health care systems in several countries are subjected to tremendous cost pressure. Mandatory discounts, price limits and reimbursement models often force manufactures to lower their costs per package. Machine and systems manufacturers have to work on improving overall equipment efficiency. In Industry 4.0’s future, this means using integrated systems with reliable availability and a continually high product quality. This is the only way to ensure that providers can keep up with a dynamic market in the long run.