Two Sidel Matrix Combis have been installed at the Sanpellegrino plant in Ruspino, Italy, increasing production capacity to meet increased global demand.
The global bottled water market is forecast to expand at a 6.6% CAGR (compound annual growth rate) over the period 2016 to 2024, rising from a total value of nearly US$170 billions to over US$307 billions at the end of 2024 (source: Transpency Market Research).
In the carbonated category Nestlé Waters' Sanpellegrino brand continues to gain ground as a premium water of choice in restaurants and homes the world over. This growth in global demand has played out in upgraded production capacity at the Sanpellegrino facility in Ruspino near the water's source in the natural springs in Val Brembana in the San Pellegrino Terme area, at the foothills of the Italian Alps.
Beverage equipment specialist Sidel has worked with Nestlé Waters for over 50 years, a relationship which has resulted in many important and significant developments within the beverage industry.
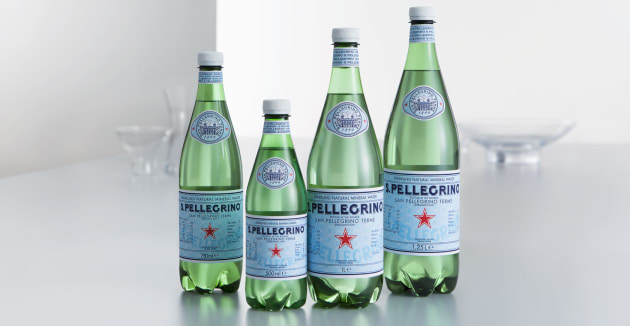
Salvatore Sbriglione, plant director at Sanpellegrino, explains: “We wanted to increase output rates according to the different bottle formats we produce in Ruspino. The line dedicated to the bigger formats – 750ml, 1000ml and 1250ml – was projected to grow output rates to 36,000 bottles per hour, while the one used to produce the 0.5 litre bottles was intended to increase speed to 54,000 bottles per hour.
"In awarding the contract to Sidel – to upgrade our existing PET lines and to increase output rates and speed – we clearly considered the longstanding relationship between Nestlé Waters, the group we are part of, and this supplier. However, what convinced us most, were the high hygiene standards offered by their solutions and the fact that we both share the same, absolute focus on product and process quality.”
Combining blow moulding, filling and capping processes into a single system, this solution reduces operating costs and uses up to 30% less floor space, compared with traditional standalone equipment. By integrating the different equipment types and production phases into a single system, while eliminating conveying, empty bottles handling, accumulation and storage, line efficiency is improved for a lower TCO (total cost of ownership).
Additionally, using fewer component machines, Sidel Matrix Combi offers 2-4% higher efficiency levels than standalone machines, faster format changeovers, lower energy consumption and a reduction of operating costs by 8-12% as a result of savings on labour, raw materials and spare parts. By handling the bottles by the neck throughout the latter stages of the production process and the elimination of intermediary conveying, it also offers greater freedom of shape and significant lightweighting opportunities.
Andrea Lupi, Sidel’s global key account director, comments: “Both Sidel Matrix Combis installed at the Ruspino facility feature Sidel’s Blendfill configuration, combining carbonator and filler in a single system for top quality sparkling water. This solution contributes to further reducing consumption of CO2 and results in a smaller footprint.”
Both Combis supplied to the Ruspino site are equipped with Sidel's SF300 FM filler, ensuring strict hygiene – via a reduced filler enclosure – fully automatic changeovers performed via HMI (Human Machine Interface), optimum uptime and highest productivity. This solution allows for a reduction in the use of CO2 and, by using servomotors, it minimises the consumption of electrical power.
Utmost precision of filling is guaranteed, thanks to magnetic flowmeters and no vertical movement of bottles. This allows smoother handling, minimal foaming and no bottle jams. Moreover, the reduced filler enclosure ensures minimum use of water and chemicals during external cleaning. This is how the Sidel Matrix Combi achieves full food safety – a major priority for Sanpellegrino.