AIP members were privy to a virtual tour of OF Packaging’s local flexible packaging converting facility based in Carrum Downs, Victoria, which delivers flexographic print packaging solutions primarily to the horticulture, pet food, produce and bakery markets through its local Plasticover business segment.
Through the tour, participants gained a better understanding of the entire manufacturing process for flexo-print, large-format packaging, and viewed the important aspects of production, which ensures the best outcomes for packaging made in Australia.
The facility highlighted in the tour is the company’s only local manufacturing and converting site for flexographic printing, laminating, bag making, slitting and pouch making.
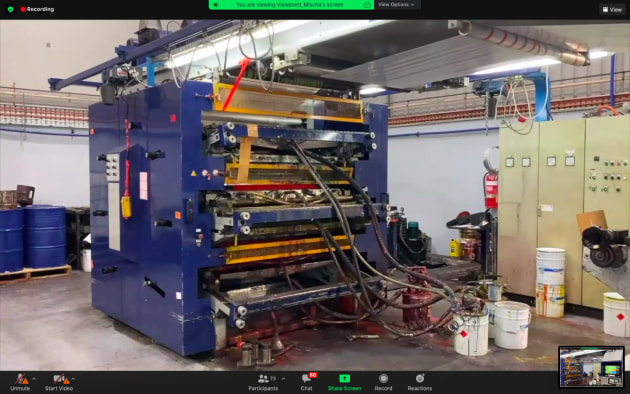
Participants were taken on a detailed walkthrough of the flexographic central-impression printer and colour management services that are available on-site, as well as both solvent-free lamination and film slitting machinery.
As for the printer used, OF Pack incorporates a flexographic printer machine, which is a 6-colour, central impression machine, meaning each printing station is mounted onto one central drum, compared to the old conventional style of stacked pressing.
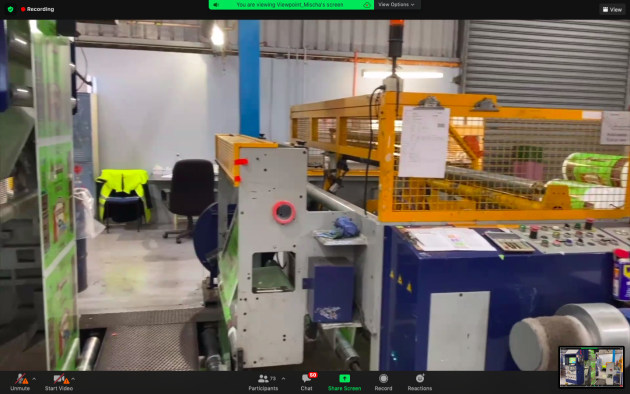
“When you look at the converting process for flexo packaging, it is not an easy process where you just have to press a button, and there are some processes that we have to follow in order to produce a finished pouch or bag,” says Joe Foster, co-founder and managing director, OF Packaging.
“There is quite a number of steps involved in the process, and each one of these steps requires a high level of expertise and knowledge to ensure the best outcomes for each individual job.
“We have to start with the artwork process, then the film is blown before going through the printing process, which we then have to inspect, before sending it off for lamination. From here we go on to slitting then to the finishing section where we make the product.”
As for whether or not the facility is already food grade approved, Foster says they are heading in the right direction to get completely certified.
“When we took over the factory 18 months ago, it was predominantly looking after horticultural products and did not require the same level of certification, as for food products. However, we are moving along with the process of getting approvals in terms of being fit for food grade and making all the right improvements to the site,” explains Foster.
“In terms of food approval, we ensure that all required processes are being followed and everything is being documented – we check all of the raw materials in-house, we conduct food safety audits independently, and we have food safety certification for all materials we use in-house.”
The tour also looked at the multiple pouch and bag converting machines, and the in-house laboratory for product testing and quality control.
As for the products being manufactured and OF Pack’s processes, questions were raised of its sustainability credentials, which Foster was proud to clarify, considering he sees sustainability as both the company’s and his own personal mission to implement.
“At the Carrum Downs factory I am proud to say that we have got a market for all of our offcuts, setup materials and trim waste material, which goes back sometimes to the film blower, or a lot of times actually back to plastic recyclers here in Melbourne,” Foster says.
“We conducted many trials and developments around mono-based polymer laminates, which are now more recyclable-friendly, for more sustainable options for our pouches and bags.
“We have the ability to make bags out of 60 per cent recycled plastics for non-food-based products, and we have manufactured pouches out of recycled materials for a couple of companies across Australia, New Zealand and one in Canada – which utilised materials up to 40 per cent recycled content.
“The refill pouches we convert are made out of fully-recyclable laminated materials, and we also currently have a number of products out in the marketplace around mono-based polymers that have already enjoyed quite a bit of success.
“Sustainability is our number one project, and we have a lot of interesting things we are working on at the moment, which are ready to roll out, as well as a number of companies in different markets utilising recycled plastic materials.”