At the Australasian Packaging Conference, a breakout session led by Barry Cosier, co-CEO of Soft Plastic Stewardship Australia (SPSA), brought together voices from across the packaging supply chain to tackle one of the sector’s most pressing challenges: how to create a viable circular economy for soft plastics.
Cosier opened the session by acknowledging the hard lessons learned from the failure of the REDcycle program, emphasising the need to keep all “four legs of the chair” – collection, recycling capacity, end markets, and funding – in balance. He made clear that SPSA’s approach would avoid the pitfalls of overpromising without the infrastructure or market support to deliver, stressing that collection must be matched by real downstream processing and offtake capacity.
Packaging in practice
David Roberts, packaging development manager at Birch & Waite, brought a brand owner’s perspective to the session. Operating as the company’s sole packaging resource, Roberts described the practical difficulties of transitioning to recycling-ready films on legacy machinery.
Running high-barrier sachets on heat-intensive, high-speed lines not designed for modern mono-material structures has caused functionality and yield issues. Melting, jamming, and excess waste were frequent challenges.
“You’ve got to make these materials work on machines never designed for them,” Roberts said. While praising tools like the PREP tool and CEFLEX guidelines, he stressed the need for standardisation and consistent specifications across the industry.
Infrastructure in motion
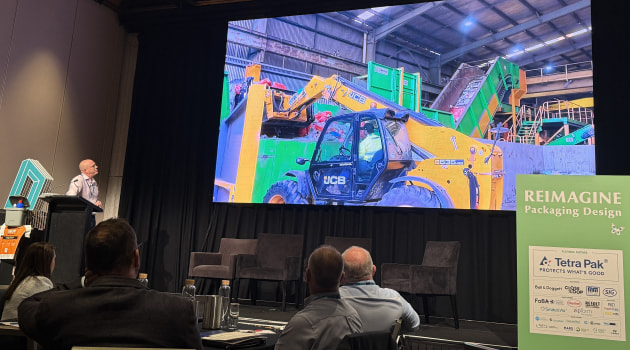
Daniel Gallagher, CEO of iQRenew, focused on the company’s investment in Australia’s first purpose-built soft plastic recycling facility, located in Taree, NSW. The SPEC processing plant – short for 'Soft Plastic Engineered Commodity' – is already operating at scale, processing around 40 tonnes of post-consumer soft plastics daily.
Gallagher said the facility could absorb the national collection volume formerly managed by REDcycle, offering a crucial “missing link” in infrastructure. He underscored the importance of traceability, noting iQRenew’s use of QR-coded bags to confirm source and destination of recovered materials. SPEC products such as flakes and pellets are already being used in fence posts, flexible films, and non-food grade packaging components.
“The infrastructure is here – we just need strong offtake markets and procurement from industry to keep it viable,” Gallagher urged.
Advanced recycling for a circular outcome
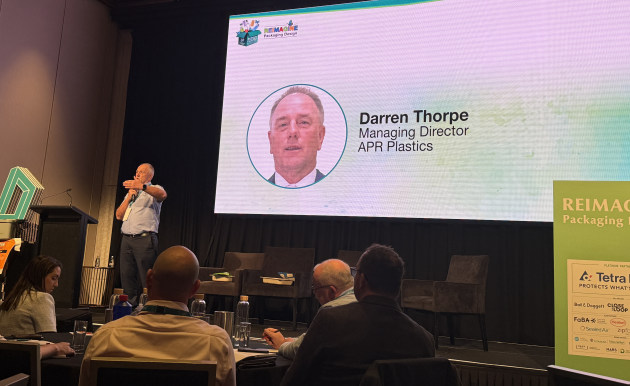
Darren Thorpe, managing director of APR Plastics, detailed the company’s journey toward launching Australia’s first commercial-scale chemical recycling facility for soft plastics. Operating on a pyrolysis-based model, the plant aims to process 3,500 tonnes annually starting in September, with long-term ambitions of scaling to 100 tonnes per day by 2028.
Thorpe pointed out that while mechanical recycling will always have a role, chemical recycling is essential for dealing with contaminated, multi-layered films not suited to mechanical processes.
“We want plastic back to plastic. This material is fit for purpose, and our goal is to make it circular,” he said.
Importantly, APR secured regulatory support from the EPA to classify pyrolysis-derived outputs as resources rather than waste – a key breakthrough for industry acceptance. Thorpe acknowledged the challenge of securing consistent feedstock and restoring community trust post-REDcycle, noting the need for clear collection systems and council engagement.
Technology at scale
Andrea Polson, stakeholder engagement lead at Licella, presented the company’s proprietary chemical recycling technology, hydrothermal liquefaction (HTL), as an efficient and scalable solution. Unlike pyrolysis, HTL uses superheated water under pressure as the reactive agent, offering energy and emissions advantages.
Licella’s technology, proven at pilot scale in Australia, has already been licensed internationally to partners in the UK, South Korea, and Japan. In Australia, the company’s proposed Altona facility has EPA approvals and is awaiting final investment decisions. Polson noted that HTL can process mixed, post-consumer, multi-layered soft plastics into oil intermediates used to make circular plastics.
However, she stressed that for chemical recycling to scale, it needs consistent feedstock and certainty from packaging regulations. “Designing for recyclability – whether mechanical or chemical – is essential to make these facilities viable. It's a systems approach requiring shared cost, risk, and reward,” she said.
Key takeaways
The session concluded with a panel discussion that cemented key themes emerging from the presentations:
1) Infrastructure is ready: Facilities for both advanced mechanical and chemical recycling are operational or imminent.
2) Feedstock consistency is critical: To operate at scale, recycling plants need clean, predictable input streams – something that relies heavily on packaging design and effective collection systems.
3) Offtake demand must grow: Without strong demand for recycled outputs, particularly from brand owners and manufacturers, the system will stall.
4) Collaboration is essential: No one company or technology can solve the problem alone. Cross-sector collaboration – from brands to recyclers to regulators – is the only path forward.
As Gallagher concluded, “If we keep going at our current rate, we’ll run out of legacy post-consumer soft plastic feedstock by December.”
The message from the panel was clear: the time to act is now, and the pieces are in place to finally close the loop on soft plastics in Australia.