Achieving circularity for plastics packaging is a complex challenge that requires bold and urgent action from industry and government, Dr Helen Lewis writes for PKN.
The need for rapid transformation of the plastics packaging value chain is becoming more evident, driven by ambitious climate change and recycling targets as well as growing community and government concerns about plastic waste and pollution. The plastics industry will lose its social licence to operate, and Australian businesses will be at a competitive disadvantage unless they can achieve a substantial shift in the way that plastics, and plastic packaging in particular, are produced and consumed.
These are just some of the key messages that emerged during two days of presentations and lively discussion at the Society of Plastics Engineers (SPE) Plastics and Circular Economy conference held in Melbourne from 22-23 November.
How do we achieve circularity for plastics packaging?
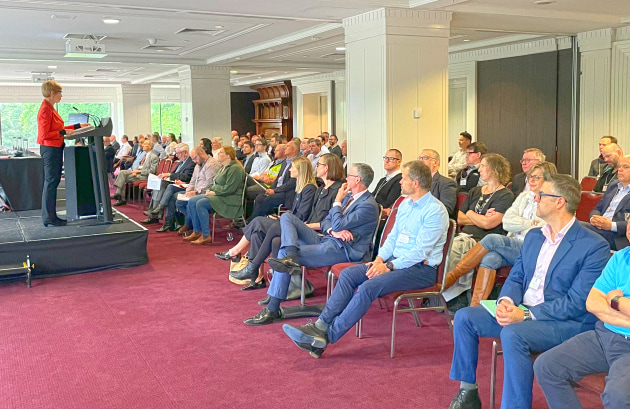
The conference program was carefully designed to focus on solutions rather than problems. With so many key decision makers from industry and government in the room, program curator Helen Millicer called for transformational change to a low emission, circular plastics industry. Several presentations on the key elements or success factors for circularity helped to highlight gaps in the current system in Australia, particularly for soft plastics.
CEO of the Australian Packaging Covenant Organisation (APCO) Chris Foley highlighted the complex nature of the packaging ecosystem, with many participants and decision points and complex interactions between them. APCO’s review of progress against the national packaging targets identified a series of gaps that need to be addressed collectively. As Foley noted in his presentation, “this challenge is much bigger than each of us – we need to get together and approach this as a system”.
Several strong themes emerged over the three days of the conference, with strong support for action in four key areas.
1. Design for reduction and recycling
Consumption was described by one participant as ‘the elephant in the room’. According to Kyle O’Farrell from consulting group Blue Environment, plastics consumption in Australia (across all sectors) is forecast to increase by 156 per cent to 9.7 million tonnes by 2050. Without a major change of direction, consumption of plastic packaging is forecast to follow a similar trend.
Packaging design is therefore critical to achieving circularity, both to reduce overall consumption, extend the life of products and packaging, and ensure it can be recovered. This was a strong message from Dame Ellen Macarthur in her pre-recorded address, which emphasised the need to design out waste before it is created.
Design for recovery is also essential if we’re to achieve true circularity. Two important aspects of this discussed at the conference were thresholds for recyclability and the role of compostable packaging.
New regulations in the European Union will raise the bar for any company designing for the EU market. Mattia Pellegrini, responsible for circular economy programs in the European Commission, reported that the existing packaging directive will convert to a regulation from 2023, with detailed and directly applicable requirements at a product level. While details of the regulation are yet to be published, it is expected to include thresholds for recyclability based on the proportion of a packaging item that can be recovered. These are likely to range from 70 per cent to 95 per cent of the packaging weight.
The potential role of compostable packaging was also discussed. During a panel discussion, both Mattia Pellegrini and Ed Kosior from Nextek reported increasing agreement in Europe that compostable packaging should only be used under certain conditions and for a limited number of applications.
2. Moving from voluntary product stewardship to EPR
In her presentation, Ellen Macarthur noted that voluntary action is not enough. She said governments need to “step up” with “bold and urgent action” to address free riders and ensure a level playing field. This sentiment was endorsed by many participants over the three days of the conference, particularly in relation to product stewardship. There was a general recognition that the time has come to shift from voluntary stewardship to EPR, particularly for plastic packaging. EPR is a policy approach (generally regulated) that extends a producer’s responsibility to the post-consumer stage of a product’s life cycle.
Rose Read from the Centre of Excellence for Product Stewardship noted that strong industry participation is one of the keys to a successful product stewardship scheme. This is possible under a voluntary scheme where the industry comprises a small number of companies (eg Paintback and MobileMuster). In most cases, however, EPR is required to address free riders. Recent statements from the Federal Environment Minister suggest a greater willingness by the Australian Government to regulate priority sectors, such as solar panels and tyres.
Mitchell Killeen from LyondellBasell International reported that the Korean Government is well ahead of Australia in this area, having introduced EPR laws for industrial and agricultural films in January 2022. Manufacturers and importers will be required to collect and recycle a certain portion or pay a “recycling charge” which will be more than the cost of recycling.
Closer to home the New Zealand Government has identified plastic packaging as one of the priority products for which a mandatory EPR scheme will be introduced. CEO of Plastics New Zealand Rachel Barker reported that her organisation is leading a two-year co-design process to develop the scheme.
The European CEFLEX program has some important lessons for any product stewardship scheme. Managing director of CEFLEX Graham Houlder outlined its ‘demand-driven’ approach to flexible (soft) plastics. He suggested that before thinking about collection and recycling systems it is important to first understand what packaging is entering the market and its recyclability, and then look at the end markets and what they require in both quantity and quality. Only then can appropriate collection, sorting and reprocessing systems be designed.
This was consistent with a strong message from Andrew Smith, executive general manager at Pact Recycling, who highlighted four elements that must be present for a plastics recycling system to work. These are:
- Raw material availability – access to a consistent supply of material at the right quality;
- Recycling infrastructure and capability to consistently convert plastics into quality resins;
- Multiple manufacturing platforms to convert recycled resins into products; and
- Demand for recycled products, including regulatory setting and procurement policies to incentivise use of recycled products.
In his view, schemes and companies have failed in the past because one or more of these elements were missing.
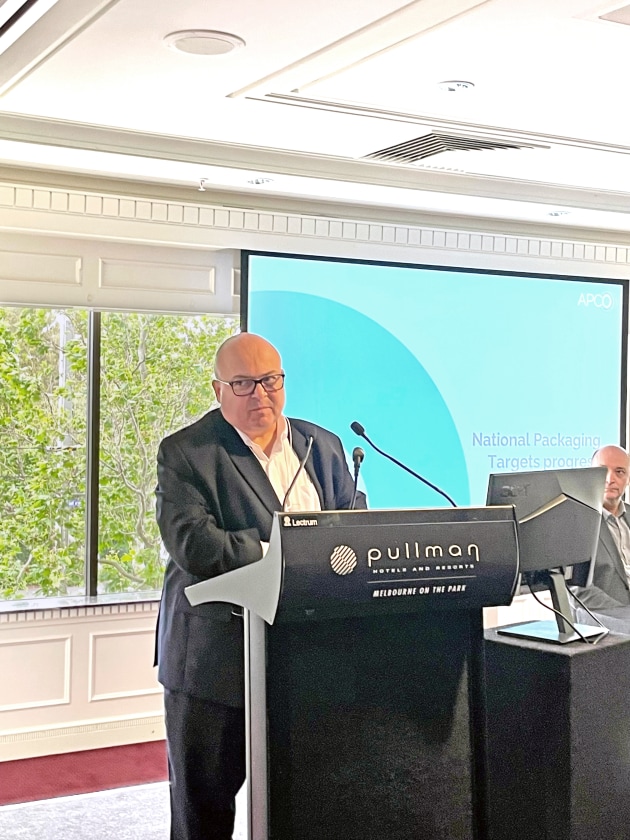
APCO’s Chris Foley noted that the policy framework for packaging is currently under review. The Federal Government is raising the possibility of legislative change, reflecting community concern about plastics and packaging.
3. Policy and regulations to align economic incentives
Andrew Smith emphasised that recycling will only work with business drivers that are economically attractive to all participants. PET recycling works, for example, because of the inherent value of the material, strong demand from brands and financial support for collection through kerbside and container deposit schemes.
Economic drivers don’t exist for many other plastics, which is why additional support is required through either regulation or stewardship. A frequently repeated comment from participants was that recycled plastics are more expensive than virgin resin and always will be, because of the additional steps required to collect the material, sort, and decontaminate it.
Economic incentives can be re-aligned in different ways. Preferential procurement for recycled products and packaging can provide the ‘market pull’ that supports the business case for investing in sorting or recycling facilities. Other options suggested by Mike Ritchie from MRA Consulting included raising the landfill levy to around $200 a tonne, removing subsidies on petroleum (and therefore virgin plastics), increased fines for illegal dumping, and continuing to support markets through grants and subsidies.
Once again, the South Korean Government is ahead of Australia in driving the economic transformation of recycling markets, with ambitious targets backed up by EPR laws and increasing disposal charges. Conference participants called for similar changes in Australia to provide a framework that incentivises investment and the diversion of recyclable material from landfill.
4. Innovation and investment in mechanical and advanced recycling
Speakers and participants agreed that we need innovation and investment in advanced recycling technologies, with a strong focus on recovery of mixed and soft plastics. The Australian Food and Grocery Council (AFGC) is leading the development of a new product stewardship scheme for soft plastics. Barry Cosier presented AFGC’s vision for the scheme, which aims to recover soft plastics back into food grade and other contact-sensitive packaging. This will be supported by a pipeline of advanced recycling facilities planned over the next few years, which are expected to have a combined capacity of at least 135,000 tonnes.
Qenos CEO Stephen Bell expanded on plans for the company’s advanced recycling facility, which is expected to eventually recycle 100,000 tonnes of hard-to-recycle soft plastics into a food grade polyethylene. This will have identical properties to virgin resin, enabling local packaging manufacturers and brand owners to achieve the national packaging targets for recyclability and recycled content. Lifecycle analysis results from multiple studies indicate that this will result in a 40-50 per cent reduction in carbon emissions compared to virgin LDPE.
Other speakers reported on innovations in mechanical recycling to support the recovery of plastics back into higher value applications. Nextek’s Ed Kosior reported that artificial intelligence systems are being rapidly integrated in European material recovery facilities to identify objects by shape, evaluate composition, drive robotic systems and identify specific packages. Digital watermarks and fluorescent markers can be added to packaging to allow it to be sorted into food and non-food grade plastics. A new technology to decontaminate soft plastics, which can remove >99% of oils and chemical contamination is also being developed. These innovations show that we don’t need to rely entirely on advanced recycling to produce high quality resins suitable for food and other contact sensitive packaging applications. A circular plastics industry will require both.
Overall reflections
It became clear over the three days of the conference that plastics circularity will require a major shift in the way that we produce and consume plastics. Among participants there was a strong sense of purpose and commitment to transform the plastics industry from a linear to a more circular system. The challenge will be to maintain the momentum to convert the knowledge, ideas and sense of purpose that emerged from the conference into real action.
This article was first published in the January-February 2023 print issue of PKN Packaging News, p28.