Sidel’s latest stretch film technology, EvoFilm Stretch, is designed to offer the beverage, food, home and personal care (FHPC) markets a new sustainable solution for secondary packaging.
Sidel is offering the new stretch film technology to “revolutionise wrapping processes”, which it says is in response to consumer trends, such as sustainability and SKU proliferation, continuing to affect distribution and production needs.
Complementing Sidel's existing packaging portfolio, the new EvoFilm Stretch achieves 90 per cent energy savings and a 50 per cent reduction in plastic film, according to the company.
Sustainable advantages
Removing the need for any heat, the wrapping technology involves pre-stretching the film and wrapping it around the primary packaging. With this advantage, Sidel says, EvoFilm Stretch reduces plastic film consumption while using significantly less energy.
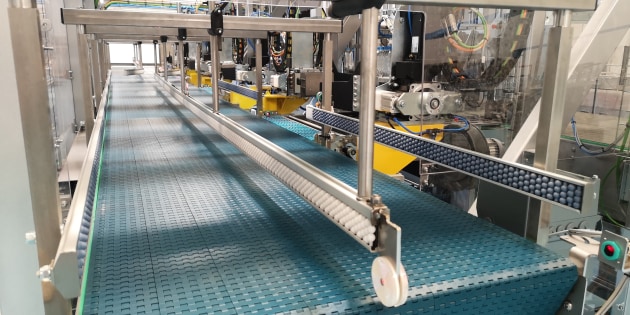
“Compared to traditional solutions, our new stretch wrapping solution is a sustainable choice for customers who are looking for alternative secondary packaging. This solution mainly targets multipacks and logistics packs, where printed film is not required, ensuring material reduction, low ecological impact and cost-savings,” said Giorgio Rocca, End of Line product manager. “With the ability to handle recycled film, EvoFilm Stretch addresses our customers’ sustainability objectives while being a competitive option.”
Meeting customer needs
Reporting speeds up to 80 packs per minute, Sidel says the new solution quickly stretches the film and applies the correct wrapping force to any packaging format. Applicable to all types of containers from 0.1 to 8 litres, in bulk or multipacks, and for a wide range of pack formats, EvoFilm Stretch is a “versatile solution which can meet the demands facing the beverages and FHPC industries”.
Maximum flexibility
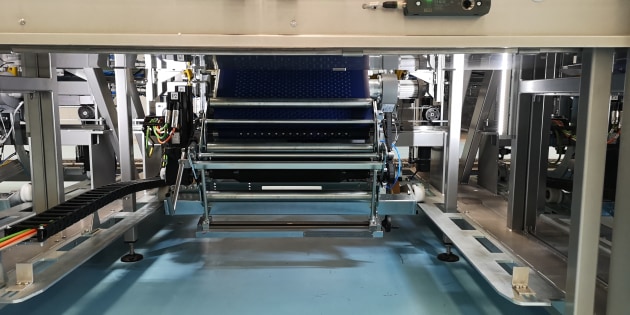
Suitable for all SKUs and primary packaging types, EvoFilm Stretch is a modular solution that can be sold as a single unit as well as part of a complete line. The technology is user-friendly and achieves a toolless manual format changeover in less than 12 minutes/module.
EvoFilm Stretch also removes the need for a shrink tunnel and tunnel discharge equipment, creating a smaller, compact operational footprint for customers.