Two Australian-owned manufacturers have partnered to deliver a manufacturing line for products in the Australian Organic Food Co range. Lindy Hughson spoke to executives at Inox and Flavour Makers to explore the scope of the project.
The ethos of Flavour Makers’ Australian Organic Food Co brand is to create a sustainable and healthy future for Australia. It has partnered with regenerative and sustainable 100% Organic Aussie Farmers to tackle complex issues around food waste, soil regeneration, and supporting the organic industry.
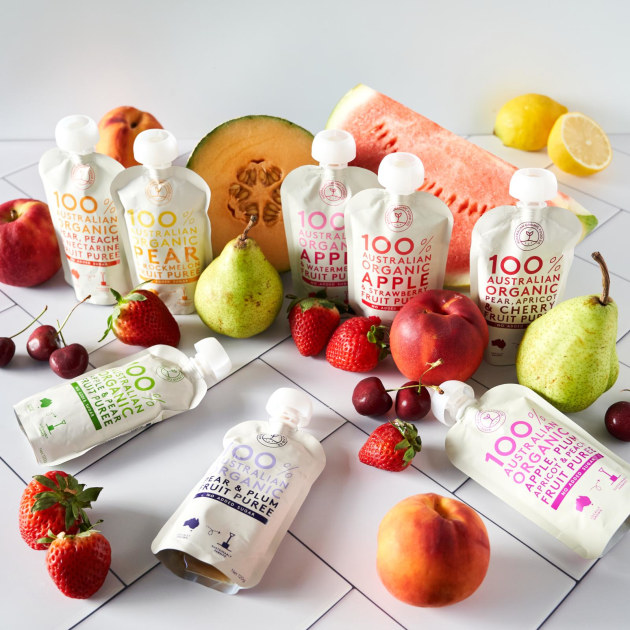
Using local equipment suppliers is also central to the sustainability tenet, and so when Flavour Makers needed to increase production capacity and processing flexibility in its manufacturing plant, it turned to Australian processing machinery manufacturer Inox for the turnkey solution.
From concept to completion, the project was 14 months in the making. A key driver for the investment, as Flavour Makers’ founder Adrian Cester tells Food & Drink Business, was increased local and export demand for the Australian Organic Food Co product range, which exceeded the existing production line’s capacity.
“We were looking to increase our daily output, reduce manufacturing costs, and become market leaders in the process,” Cester says.
Inox was tasked with designing a complete process system to manufacture baby food and on-the-go breakfast products packaged in spouted and stand-up pouches. The system included mixing, cooking, delivery, and clean in place (CIP) for two filling lines.
“For Inox, the scope of the project included process design, equipment design, complete equipment manufacture, automation, installation and commissioning, and support of a complete operating food process plant,” Rob Becher, MD of Inox says.
The equipment line-up features several Inox flagship products, such as its Instantiser for high speed, high shear mixing; Contra-chef and Maxi-chef kettles for cooking; as well as Inox’s CleanCIP automated CIP system.
Becher explains that all other ancillary equipment was also manufactured by Inox, including the operating platform, pallet receival, bulk liquids receival and supply, holding tanks, heat exchangers for cooling, all process pipework, pneumatics, and the PLC control system.
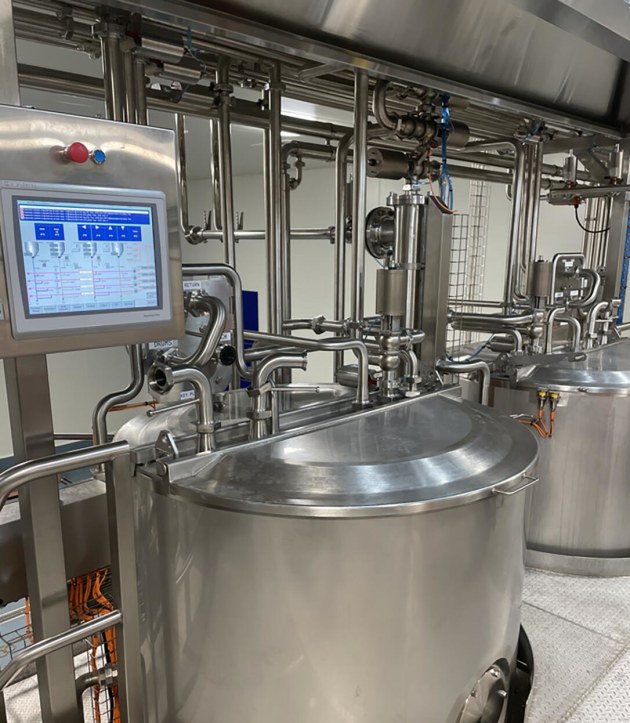
Following the successful commissioning of the lines, the process can achieve a batch volume of 4000-5000kg per hour.
Focus on flexibility
The manufacturing process followed is relatively simple. Ingredients are placed into kettles for blending according to the recipe. The blended and cooked product is emulsified until consistency is achieved, and then it’s sent to the filling machine to be packed into spouted or stand-up pouches. But while the process is simple, flexibility was a key requirement for Flavour Makers.
“The system had to build in process flexibility to allow Flavour Makers to use the lines for other products, both present and future,” Becher explains.
“The processing challenges related to some products requiring heating or cooling, and/or emulsifying as well as providing a certified and validated CIP program for the entire process line and all of the equipment,” he says.
“Overcoming these challenges was a function of smart process design practice drawing on decades of food processing experience on the part of Inox engineers, as well as using technology that is available today from our key suppliers, including pump and valve selection and high-end automation programming techniques,” Becher says.
Cester says, “The purpose-built production room now has the flexibility to also manufacture sauces to be used in soups or other food products, along with private label brands, and leading organic brands such as our own award-winning Australian Organic Food Co brand.”
For both companies, the completed project is understandably a source of pride.
“We are proud of the fact that all of the equipment supplied on this project is completely made in Australia by Inox. We are proud of the level of quality we achieve, the state-of-the-art processing design and integration, and the reliability that our equipment offers,” Becher says. “It is satisfying to work with a company as great as Flavour Makers, and especially so, being such advocates of Australian manufacturing.”
Cester says, “We believe the future of food in Australia is organic and regenerative agriculture, so through both manufacturing for others, and our own brands we have developed and continue to develop the option of a regenerative organic supply chain.”
Working with Inox, Flavour Makers has achieved the flexibility and increased capacity outcomes it was looking for, putting the company in prime position to strengthen its leadership in the organic foods market.