Could this be the southern hemisphere's biggest depal? At nearly nine metres high, Foodmach's latest high-level depalletiser for a beverage client must come close.
This high-volume giant includes a 183m2 platform on a heavy steel frame and is construction-welded and bolted for strength. It was built by the Foodmach team to provide the customer with rapid depalletising of a range of containers with fully automatic changeovers, no tools or parts required.
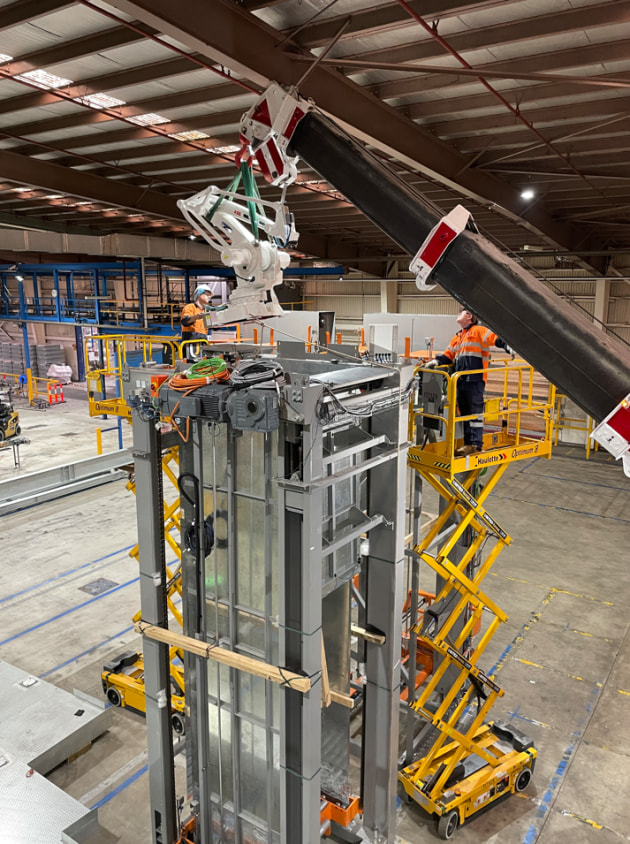
Offering speeds of up to four layers/min, it features four-sided containment of the layer to ensure container stability. It is designed to minimise friction and provide the 'shh' factor: low-noise operation at less than 75dB.
An ABB IRB460 industrial robot on a pedestal, fitted with vacuum grippers, picks up the dividers and top frames and places them in their respective magazines. Utilising an industrial robot reduces the number of devices needed to be maintained and eliminates vertically installed pneumatic cylinders.
The pallet hoist is controlled via a shaft encoder and frequency inverter with dynamic braking facility to give accurate positioning and high-speed pallet changeovers.
Can-specific indexing heights are saved and available for selection on the depalletiser operator interface setup screens. The four-chain pallet hoist carriage has levelling adjustment to ensure the layers are transferred smoothly over the accumulation conveyor dead plate.
Hoist lock devices are fitted to eliminate the need to insert locking bars under the hoist carriage when personnel are entering the machine. The layer sweep design ensures no falling cans.
This machine provides all the benefits of a ceiling-height bulk depal with the convenience of a floor-level depal, including on-floor controls. It addresses the customer's sustainability requirements, using the latest servo technology and variable speed drives.
The project included significant site works for strip out of the customer's old depalletiser, relocation of other major machines and installation of the new Foodmach depal and conveyors that run from the depalletiser to case packing.
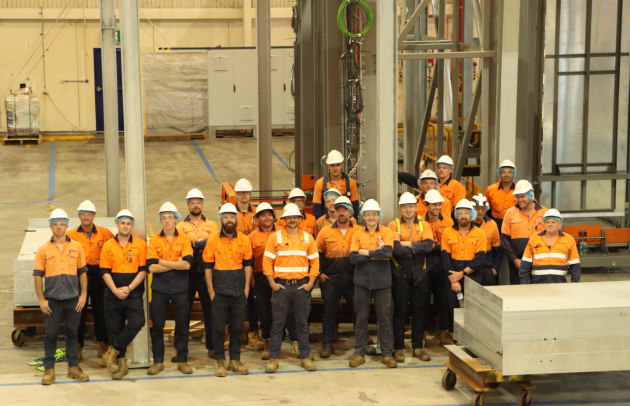