Food product recalls are on the rise in Australia. According to Food Standards Australia New Zealand, a body that co-ordinates and monitors food recalls in Australia, there are on average five official food recalls each month.
This figure does not include the many more voluntary product withdrawals.
More than one-third of all food recalls are because of non-compliant labelling issues, with undeclared allergens the main concern.
Current production trends include shorter runs of multiple variants, reformulated versions of established products and redesigned packaging. All these factors have a significant impact on labelling and require manufacturers to have greater pack accuracy. Particularly, inadequate attention to labelling has led to many mistakes being made.
Food recalls are not only costly, they can destroy a new product or may cause long term damage to brand reputation and sales.
Product withdrawals can cost companies hundreds of thousands of dollars – but the brand damage on top of that cannot easily be calculated.
Mistakes often happen when people are under pressure and corners are cut. Effective and integrated plant automation can play a lead role in minimising costly and damaging recalls. With the right support and effective compliance systems, many food recalls can be avoided.
No silver bullet to eliminate all threats
Firstly, it’s important for food processors to keep abreast of changes to regulations.
A basic requirement is that both pre-printed and variable data (including best-before dates) must correlate correctly with the product inside the pack.
While there is no single silver bullet to eliminate all these threats on an enterprise-wide scale, there are many production-level checks which can be integrated into control and information systems. Taken together, they can dramatically – and reliably – reduce the risk of recalls.
A common type of production line includes primary packaging (robotic pick-and-place and tray sealing), secondary packaging (top-load cartoning), and tertiary packaging (case-packing and palletising).
There are several points at which faults can occur, with the potential to trigger a recall.
The servo-driven tool lift on the tray sealer could be drifting over time, or seal quality could be compromised by imprecise temperature control or a change in packaging substrate. With the pick and place, items may be missed out of a multi-component pack.
At the check-weighing and coding stage, the scales may be set up for the wrong pack size.
All functions can be managed from a single control system
Even when the overprinting is correct, the wrong product label may have been loaded into the labeller. At the end of line, item codes may not marry up with pallet codes.
Surprisingly, perhaps, all these functions could be managed and monitored from a single control system. Vision systems for verifying packaging, product and codes, temperature control, sensors, and robot controls can all sit on a single machine control platform with direct two-way, real-time connectivity with factory or enterprise-level databases.
The installed price of vision systems may have prompted potential beneficiaries to treat this technology with caution. But that perception is changing, with end users and machine builders increasingly choosing to fit vision systems on their lines. Furthermore, regulations are increasing, demanding the capabilities that vision systems provide.
Vision will verify codes, graphics (reconciling each pack with the product on the line), pack components, label presence, print legibility, shape, colour, and optical character recognition (OCR) at even the highest line speeds.
Database connectivity means that quality inspection and production data can be gathered, and traceability and regulatory compliance can be ensured. It allows data to be analysed for adverse trends and to trigger predictive or preventative maintenance. Traceability helps confirmation the authenticity of an article, its route to market and in the tracking down of counterfeit goods.
Through advanced technology industry can minimise risk
The individual machine controller can offer this level of connectivity while bringing under one umbrella logic, motion, vision, safety and robotics.
There is no reason why the food industry could not follow the example of the pharmaceuticals sector in embracing automation at this high level, for reasons of efficiency and flexibility but also – increasingly – to minimise the risk of product recalls.
Through advanced technology, the food processing industry can minimise product recalls, increase productivity and improve workplace safety.
Omron, a global leader in automation technology, offers a range of automation solutions designed to improved productivity in the food processing industry – and avoid costly recalls.
Omron’s latest technology addresses major issues such as quality control, improved efficiency and productivity, worker safety, traceability and operating simplicity.
For example, new advanced visual inspection systems can perform a broad range of product inspection tasks including:
- label inspections;
- barcode reading;
- label or product damage;
- character recognition;
- counting;
- shape recognition; and
- positioning of products.
Ground-breaking new vision system using AI to detect defects
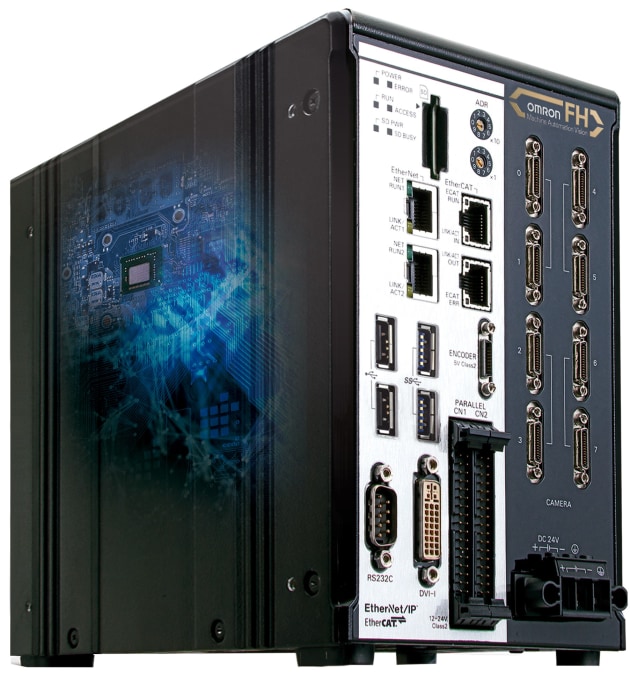
Omron recently has released its latest FH Series Vision System with the industry's first defect detection AI technology that identifies subtle defects with “human-like” sensitivity.
For many industry sectors, particularly food and beverage, it is vital to reliably identify subtle defects even on flexible lines producing a wide range of items.
The new artificial intelligence (AI) technology reproduces the techniques of skilled inspectors to reliably detect defects that were once difficult to capture, automating human vision-based visual inspection.
The new AI is now part of the FH Series Vision System to maximise the inspection capability.
An AI Fine Matching tool learns from the image data of non-defective products to quickly acquire the “expertise” that inspectors develop over the course of many years. This reduces costs and boosts productivity through automation.
With Omron Vision Sensor Technology food processors can:
- eliminate human error;
- increase productivity with high speed production lines;
- reduce waste;
- enhance company reputation and customer satisfaction;
- avoid costly product recalls; and
- get a quick return on investment.
And by using mobile and collaborative robots food processors can:
- improve quality;
- achieve greater accuracy and precision;
- eliminate contamination;
- increase productivity; and
- improve workplace safety and risk of injury.
Also, traceability has become an essential part of the food processing supply chain.
By using big data and IoT (internet of things), products can now be tracked from paddock to plate.
With improved traceability technology businesses can now prevent counterfeiting, achieve higher throughput, better quality, and lower costs – with less wastage and pollution.
The big advantage of using Omron vision technology is that all data can be collated using one controller. The information can then be monitored internally or externally by a remote smartphone or tablet.
With Omron’s Sysmac system using an NJ series controller you have a total automation system. Sysmac integrates control, motion, safety, robotics, and sensing technologies into one platform.
Omron is a member of the Australian Packaging & Processing Machinery Association (APPMA).