Some 25 years ago, Coopers Brewery in Adelaide commenced a journey from mechanisation to automation – which has resulted in outstanding productivity improvements. Hartley Henderson writes.
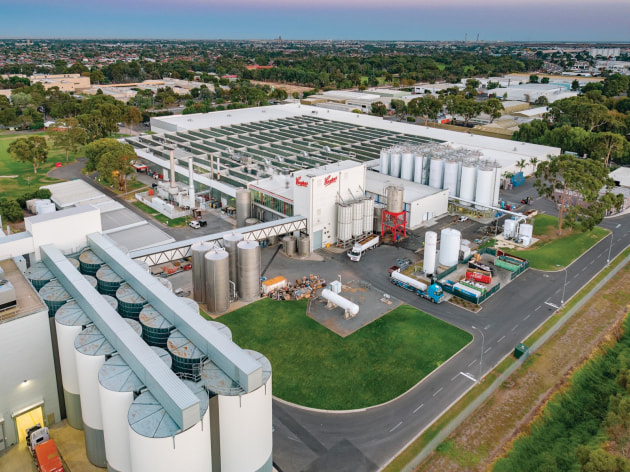
Founded in 1862 by Thomas Cooper, the company is the largest family-owned brewery in Australia. It is an unlisted company with more than 170 shareholders, most of whom are related by descent or marriage to Thomas Cooper.
With a total workforce of 230, including interstate and overseas employees, Coopers currently represents about five per cent of Australia’s total beer market and sells around 80 million litres of beer a year.
In 2001, the company built a new brewery on a 10 hectare site in the Adelaide suburb of Regency Park at a cost of $40 million; more than $150 million has since been spent on increasing capacity and warehousing.
In 2017, Coopers opened a $65 million malting plant at its Regency Park site with a capacity of 54,000 tonnes per year, of which the company uses about a third. The rest is sold nationally and overseas.
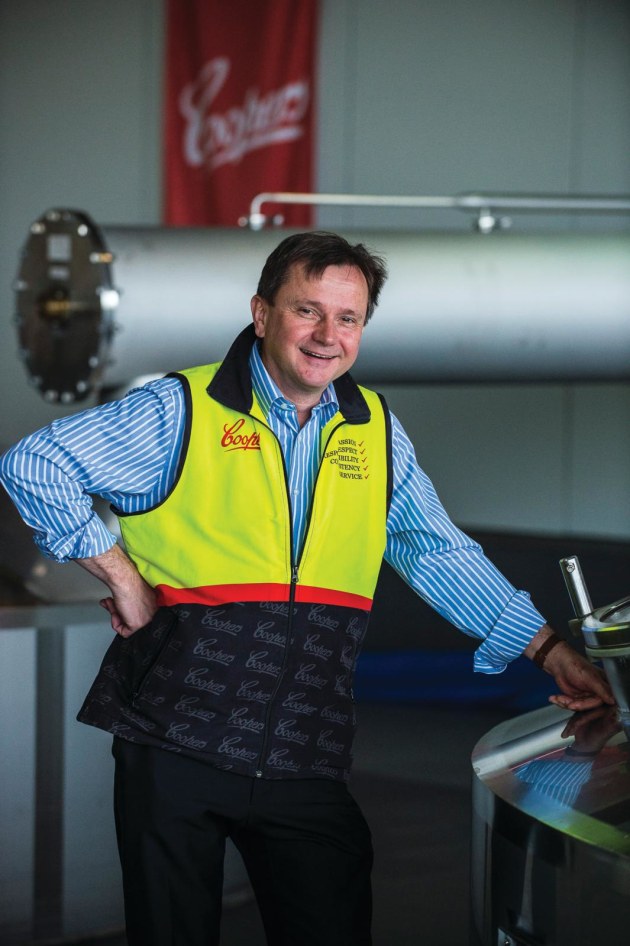
Coopers operations manager, Nick Sterenberg, says the automation journey over 25 years has delivered substantial productivity improvement of around 800 percent in relation to the number of cartons produced per operator. “We started with just two PLCs and that has grown to 70 PLCs which automate various parts of the plant,” he told PKN at a recent interview in Adelaide.
“Manufacturing processes now are generally going to smaller batch sizes and this means more changeovers, increasing complexity, and the need for more pieces of information. With the introduction of advanced monitoring and analytical technology, things that were previously done in the laboratory are now done on the line in real-time.”
Sterenberg compares the Coopers facility to a big machine, which is controlled by PLCs via a SCADA system.
“In relation to packaging, each production run is a work order that starts and stops down on the line, and all operational information is collected directly from monitoring devices on the line.
“This information shows the efficiency of the line, including how fast the bottles run and any wastage, such as bottles falling over. The data shows you any issues with the line, enables quick remedial action, and reduces downtime,” he says.
Another key benefit of automation, says Sterenberg, is that it has enabled traceability of all products from the farm gate to the bottle shop.
“We have an in-house automation team that works closely with Siemens, which supplies most of our automation technology. This partnership follows the steps necessary to introduce effective automation systems for the company including identifying areas for improved productivity, creation of a Functional Design Specification (FDS), and establishing user requirements.
“Once deliverables have been identified, an Australian Standard Contract is prepared and Siemens is provided with an order to deliver to specifications. Siemens then builds a test system and delivers it to us so any bugs can be ironed out before becoming fully operational,” he says.
Automation phases
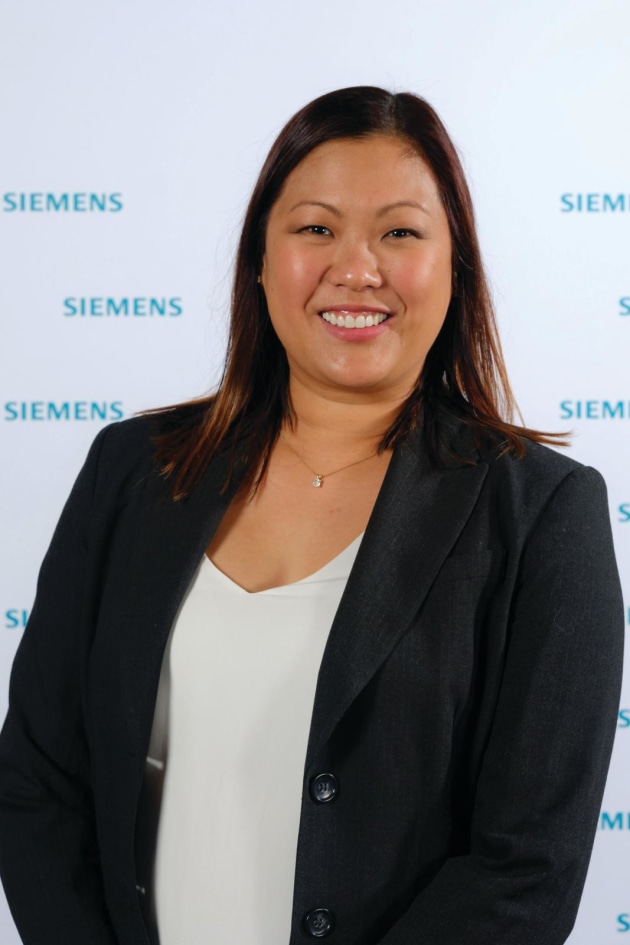
Leonie Wong, business development manager at Siemens, says the Coopers brewhouse was commissioned in the late 1990s with Siemens controllers, and it became the standard automation platform as the plant grew.
“In around 2007, the Siemens OpCentre SIMATIC IT LIMS (laboratory information management system) was introduced as a quality management system, replacing Excel based tools to manage laboratory data.
“In 2011, the MES (manufacturing execution system) was deployed for the filling and packaging part of the plant, then in 2014 it was deployed to the brewing and process sections. This gave Coopers a recipe management system and helped with production management,” she says.
Siemens PCS7 operates the brewhouse and, together with the LIMS system, Coopers has precise quality control and increased transparency of its processes, says Wong.
“The LIMS links laboratory test information with batch production data so they can ensure product sent to packaging meets their strict quality requirements.
“The various filling and packaging lines interact with the MES, which helps with complete transparency of data and gives a clear indication of the performance of the lines. This in turn helps with continuous improvement initiatives.
“For example, in most cases the empty bottles are delivered right to the depalletiser, which increases efficiency over being staged in a warehouse holding area before being moved to the depalletiser,” she says.
Wong says that by providing significant increases in efficiency and the repeatability of delivering a high-quality product, automation can help greatly in managing the costs of production.
“The MES is also linked to the AGVs (automatic guided vehicles) to alert that a full pallet of product is ready to be collected by the AGV and moved to a storage location,” she says.
Outstanding benefits
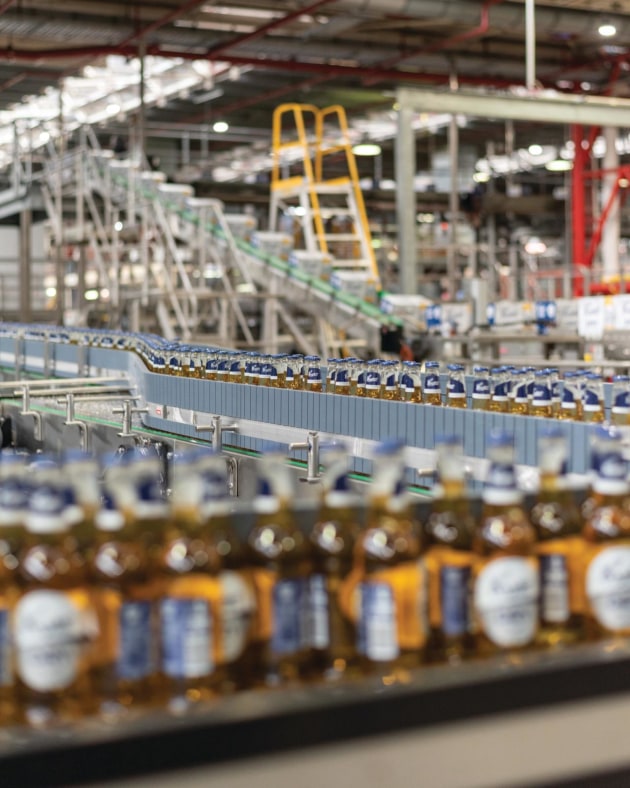
Nick Sterenberg says it is clear that automation has delivered a range of substantial benefits for Coopers – in particular, human productivity has increased and costs have gone down.
“Humans just can’t do some aspects of automation, and we have gone from systems as good as a person to systems better than a person. However, even with automation, there is a need for good quality people to get the data in, analyse it, and initiate any necessary action.
“With the huge pace of change, there have also been some challenges along the way, which mainly related to the need for people to adopt new ways of doing things; however, this has largely subsided and people are now more accustomed to change.”
Sterenberg points out that following the mechanisation and automation phases of Coopers’ journey, the company is now moving into a digitalisation phase as part of the fourth industrial revolution (Industry 4.0).
He believes that like automation, this can be a stepped process, and companies do not have to try everything at once. He emphasises the scalability of Industry 4.0, saying it is not just for big companies.
“Rather than a ten-year plan, we have a regular improvement process that identifies any issues and opportunities for improvement.
“The focus is on doing the do-able and taking small steps to ensure that new initiatives are bedded in effectively,” he says.