To fund its expansion and support its mission to eliminate expanded polystyrene (EPS) from the supply chain and our oceans, multiple award-winning innovator of the Woolpack packaging concept, Australian-owned company Planet Protector Packaging has launched a crowdfunding campaign with a target of $3 million.
Planet Protector Packaging celebrated World Ocean Day this week by launching its crowdfunding campaign. Since its establishment five years ago, the company has been on a mission to save the ocean from expanded polystyrene by replacing it with Woolpack, its sustainable packaging solution that uses sheep wool waste as an insulation in packaging designed for shipping perishable products.
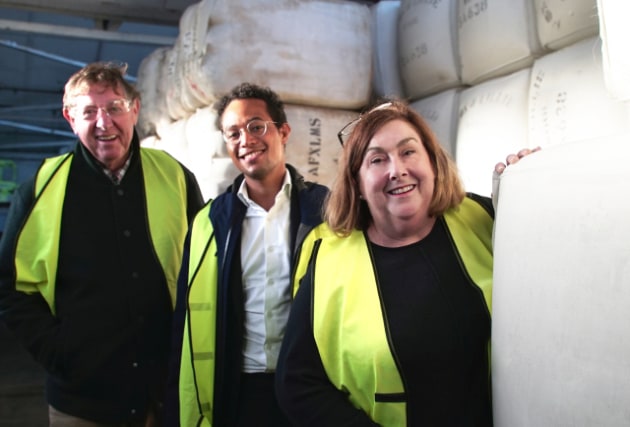
With annual revenues over $5 million, the company is poised to scale and will invest the money raised into expanding its operations. Plans are to build a wool manufacturing facility in Geelong, VIC, Australia’s wool capital, bringing this step of the processing back onshore.
In the absence of wool processing capability in Australia, Planet Protector Packaging has had no choice but to send waste wool to China for processing. Bringing wool processing back home, the company says, will create jobs, support regional communities and farmers, and create a 100 per cent sustainable alternative to EPS.
oanne Howarth, Planet Protector Packaging’s founder and CEO, said, “We use waste wool that is destined for landfills and we create environmentally responsible packaging that replaces expanded polystyrene in packaging supply chains. It gives sheep farmers another income stream, stops filling our landfills, and saves our oceans. For our clients, it is another way they can tick the environmentally responsible box and this is what all businesses are looking to achieve as the world transitions to a circular economy.
“When I meet people and explain our product, they always ask me how they can invest. It makes sense for us to crowdfund the next big step for the business by offering this to all Australians. We would like to involve as many as we can in bringing manufacturing back to Australian shores. Innovation is the only way to make that happen,” Howarth says.
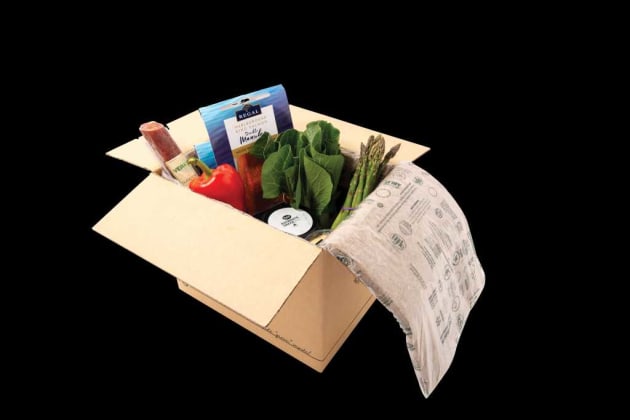
To date, Planet Protector Packaging has replaced over 7.5 million polystyrene boxes with its Woolpack packaging and its customers include many iconic brands such as Blackmores, Baxters, The Dinner Ladies, and more.
You can find more information on this crowdfunding opportunity here. Planet Protector’s expression of interest period commenced on 8 June, 2021 with the funding round starting on 29 June and running through to 19 July, 2021.