In a major boost for the uptake of Packamama’s eco-flat rPET wine bottles in Australia, the company has opened a new bottling facility in Cudal, NSW, in collaboration with Tamburlaine Organic Wines.
Packamama, which has already won several awards for its eco-flat rPET wine bottle, says it is focused on the Australian market as it believes the scope for innovation in wine bottle packaging represents a massive opportunity.
Speaking to PKN shortly after the new facility launched, Santiago Navarro, CEO & founder of Packamama, said, “Australian wine is a 1.7 billion bottle-units per annum market of amazing wines with broad appeal, both domestically and internationally. Unfortunately, wine faces challenging headwinds. We believe that stand-out packaging represents a rare opportunity for Australian wine to leverage Packamama’s innovative bottles in the way it did with screw cap years ago.”
Navarro said the company has early-stage plans to reach a seven-digit annual volume within its first couple of years, and at the current pace, it is confident in achieving this goal soon. He added, “Our motivations are for nine-digit volumes, and we believe this is achievable. After all, nowadays screw cap closes nearly all wine bottles in Australia, so why should better bottles, as offered by Packamama, not accompany better closures.”
The new facility, located in Cudal near the wine heartland of Orange, will serve as a contract packing hub, allowing wine producers, brand owners, or retailers to leverage Packamama's eco-flat bottles in Australia – provided they can send their wine in bulk to Cudal. The collaborating partners say this inclusivity will ensure that this bottling facility remains accessible to a broad spectrum of industry participants, contributing to the advancement of the Australian wine sector.
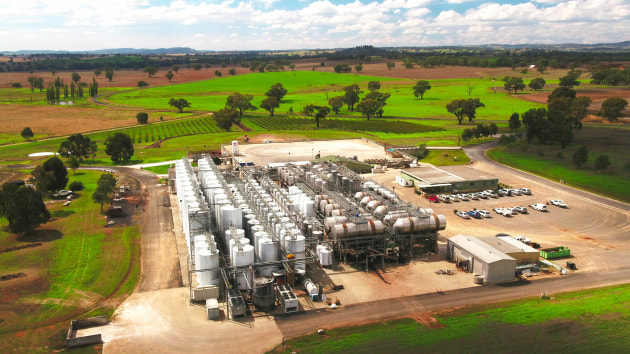
The eco-flat bottling plant forms part of the purpose-built Cudal winery, which has been a cornerstone in supporting the region's wine production expansion over the past two decades. According to Packamama, the name Cudal, with its potential origin from an Aboriginal word in the local Wiradjuri language meaning ‘flat’, holds particular relevance as well as cultural significance, adding a “unique dimension” to this project.
ADVANCED TECHNOLOGY
The new plant is equipped with a GAI monoblock bottling line, which was installed in the second half of this year. The newly commissioned line has already packed 100,000 Packamama bottles, and has a filling speed of around 4000-4500 bottles per hour.
The Italian manufactured GAI monoblock line features advanced functionalities like nitrogen purging before filling, a 32-head filler, and Novatwist application with nitrogen in the headspace before capping.
Tamburlaine told PKN it had contracted industry machine supply specialists Wine Industry Services (WIS) to work with all parties, including Packamama, to ensure the equipment was fit for purpose. WIS was also present during the launch bottlings to ensure quality deployment.
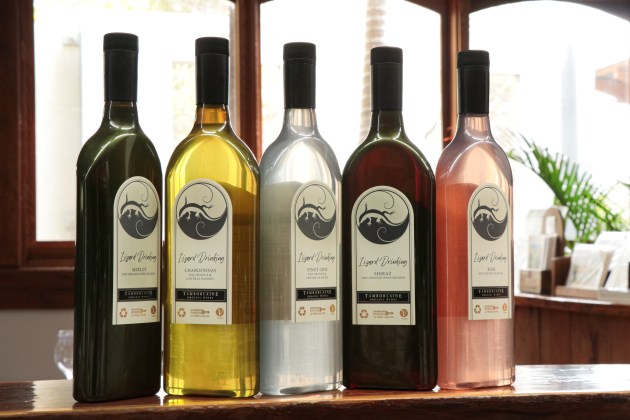
More Italian machinery features on the line in the form of the precision labeller from industry leaders Cavagnino & Gatti, which allows for accurate label positioning across the panels (with a flat panel, it is an additional requirement to get placement spot on). The newly-installed labeller accommodates a variety of bottle shapes and sizes.
End-of-line functionality is also highly automated. The overpacker is new equipment from Hamson Engineering in Canada. Tamburlaine says it works efficiently to pack the 12-bottle cases and prepare them for automated palletising. The palletiser is legacy equipment that was integrated into the process flow.
The first brand to roll off the new line in Packamama’s eco-flat bottles is Tamburlaine’s new Lizard Drinking organic wine, which has launched in October to positive market acclaim.
“Since launching our first rPET packaged wine range, the customer response at our cellar door, once they handle the product and taste the wine quality, is overwhelmingly positive. This is in stark contrast to the initial low rate of consumer acceptance of screw caps versus cork more than 20 years ago. After commissioning the new line, the first runs were impressive, achieving necessary commercial speeds and delivering wine quality in the bottle,” said Mark Davidson, managing director and head of Grape & Wine Production at Tamburlaine Organic Wines.
Santiago Navarro, who was present for the bottling over several days, just over a month ago, of some of Tamburlaine’s wines and also wines of another of their customers, added “It is motivating to see how a new bottling line designed specifically for our bottles can run them through smoothly, speedily, and consistently. We are looking forward to collaborating with Mark and his team at Tamburlaine to leverage their facility to accelerate our growth in Australia.”