Materials handling company Combilift recently marked its 25th anniversary. From a partnership between two friends to a global company with 800 employees, there was a lot to celebrate. Kim Berry visited Combilift HQ at Monaghan, Ireland, courtesy of the company, to experience the business first-hand.
[Combilift will be exhibiting at APPEX on stand A172]
Martin McVicar and Robert Moffett started Combilift after mutual success at Moffett’s company, Moffett Engineering.
Moffett had designed and manufactured the first truck-mounted forklift, the “Moffett Mounty”, which revolutionised the materials handling industry.
Not to be outdone, McVicar, who had left school at 17, was studying engineering modules through Open University while working. He had joined the company for work experience but was the company’s chief engineer before he turned 20.
I sat down with McVicar and other members of the team at Combilift’s headquarters in Monaghan, Ireland, over the course of three days of the company’s 25th birthday celebrations.
Combilift entered the market with the C4000 model – the world’s first internal combustion engine, all-wheel drive, multi-directional forklift. Its point of difference was that it didn’t need suspension. Combined with the internal combustion engine, the unit could be used inside and out.
Today, Combilift’s top five markets are the US, the UK, Germany, France, and Australia. It makes around 10,000 machines a year, which are all built to each customer’s specifications, and in March, celebrated the production of its 75,000th truck.
Combilift’s first employee, and still with the company, Mark White, worked with McVicar and Moffett on the machine, initially in his lounge room.
“We enhanced the multi-directional capabilities and established space and safety as our main priorities, as they still are today.
“The culture within the company is a very can-do attitude. From senior management right through the company,” White says.
McVicar says that can-do attitude came from the very early employees’ approach to projects which then embedded into the foundation of the company.
It took the company 350 employees before it set up a HR department.
“The HR function is more into facts and figures, rules and regulations, what’s possible, and what’s not, rather than giving people the freedom to be as creative as possible.
“The challenge is keeping that creativity without becoming too systematic as we grow our staff more and more and overseas,” McVicar says.
White says the company also still embodies continual development, with its salesforce ensuring what customers want is top of mind.
“We have to know our market to ensure our designs have value. We also protect all our designs with patents and design copyrights, which give us a leading edge over our competitors,” he says.
The company currently has around 140 patents worldwide.
Entering new markets
During anniversary celebrations, Combilift launched its first foray into autonomous guided vehicles (AGVs), which it sees as a slower growth market.
“This isn’t just about us building the vehicle, that’s just one part of the jigsaw. It’s about integrating it into the customer’s warehouse management system and software. If a business says it wants automation, but hasn’t optimised its internal systems, and you bring in an AGV, you will lose efficiency rather than gain it.”
Littlewood added that many Australian warehouses and manufacturing facilities or distribution centres are in older buildings.
“The implementation of automation or AGVs into those sites is going to be very difficult and expensive because the necessary infrastructure is just not there,” Littlewood says.
Australian presence
McVicar acknowledges that when it comes to the food and beverage sector, Combilift has a closer relationship to the third-party logistics (3PL) companies distributing the products than the manufacturers themselves.
“But we’ve noticed a model developing in the UK and across Europe where the 3PLs are building premises beside the food and beverage manufacturing plants,” he said.
Littlewood agreed, saying similar structures were happening in Australia.
“There is a lot of potential for Combilift in the food industry in Australia, we’re already working with some of the global companies like Unilever,” he said.
One industry the company is doing a lot of work in is pet food.
“We’re seeing rapid growth in that market segment because the product is heavy, the manufacturers need to store volume and they need selectivity for shelf life. The Aisle Master adds tremendous value for these companies,” McVicar says.
Combilift has also made inroads with packaging companies through existing and established connections with operations in other countries.
Sustainable future
Every year, Combilift reinvests seven per cent of its revenue into R&D, with a focus on electric powered equipment. McVicar says nearly all the vehicles it brings to market are electric, but sustainability goes beyond the machine.
“We are very focused on making our vehicles more environmentally friendly. But it moves beyond that to asking how we can enable our customers to make their warehouse utilisation more environmentally friendly,” he says.
Combilift provides free warehouse design to new customers.
“We bring tremendous value to a company with that service because it shows them how they can make their business more sustainable,” White adds.
The company is also in the early planning stages of turning its original factory into a refurbishing and recycling plant for older machines.
When asked about what the future holds, McVicar says, “We haven’t saturated any industry or market, there’s room for growth with the major DIY stores but it is also smaller distributors and single store companies who don’t know about our products or the value they could bring to their business.
“There is still so much opportunity for us globally. And, if Combilift maintains its innovation, creative, and customer-centric culture, the rest will fall into place.”
This article was first published in the November-December 2023 print issue of PKN Packaging News.
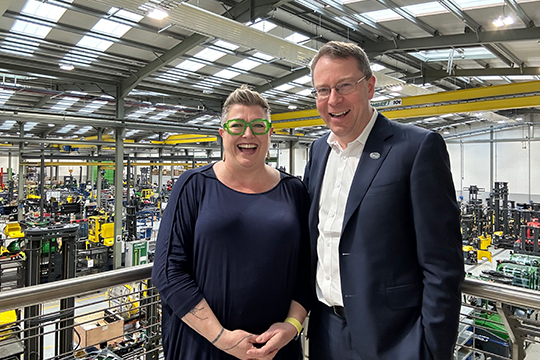